Jacket manufacturing is a complex process that involves a careful blend of creativity, craftsmanship, and industrial know-how. Whether you’re looking to produce a stylish winter parka, a functional rain jacket, or a high-performance sports jacket, understanding the entire manufacturing journey—from design to delivery—is key. This guide will take you through the different categories of jackets, suitable fabrics, essential manufacturing processes, and the critical considerations that influence the final product.
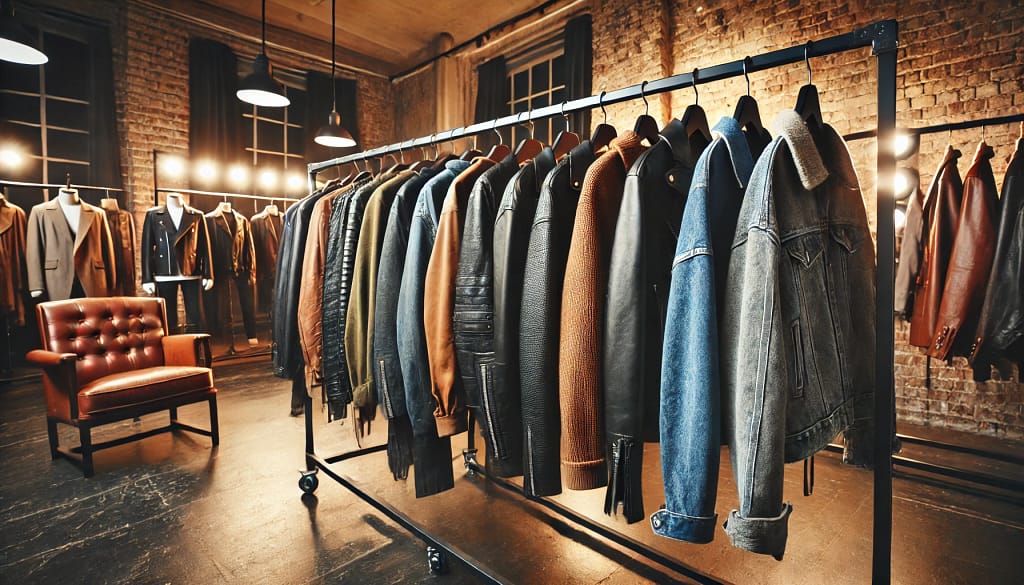
Key Considerations Before Designing a Jacket
Designing a jacket is not just about aesthetics – it’s about creating a product that meets the needs of the target audience, fits within a specific budget, and functions effectively for its intended purpose. Before starting the design process, here are some key considerations to keep in mind:
1. Target Audience
Understanding who will wear the jacket is crucial. Different demographics have different needs and preferences when it comes to jackets.
• Considerations:
• Age, gender, and lifestyle (e.g., outdoor enthusiasts, office workers, students, fashion-conscious individuals).
• The type of jacket needed: Is it a functional jacket, like a parka or rain jacket, or a more fashion-forward piece, like a bomber or blazer?
• Price point: Are you designing a luxury jacket, an affordable fashion piece, or a workwear-style item?
• Example: A jacket designed for teens might focus on style, comfort, and affordability, while a jacket for hikers might prioritise weather resistance and durability.
2. Climate and Usage
The climate where the jacket will be worn plays a huge role in the design. You need to consider how much warmth, breathability, and water resistance the jacket will need to provide.
• Considerations:
• Cold Weather: Jackets for winter should offer adequate insulation (e.g., down or synthetic fill) and water resistance for snow and rain.
• Mild Weather: For spring or autumn, lightweight, breathable fabrics may be used for comfort and light protection.
• Rainy or Windy Conditions: Windbreakers or waterproof jackets may be needed, with features like hoods, taped seams, and windproof fabrics.
• Example: A rain jacket may need to be made from a fabric like Gore-Tex, which is both waterproof and breathable, while a winter parka requires a heavy, insulated material like wool or synthetic fill.
3. Material Selection
Choosing the right fabric is crucial for ensuring the jacket performs well and looks good. The material not only affects the feel of the jacket but also its durability, functionality, and overall appearance.
• Considerations:
• Functionality: Will the jacket be exposed to harsh weather? Should it be lightweight or insulated? Do you need waterproofing or flexibility?
• Aesthetics: What texture and finish do you want the jacket to have? For example, a leather jacket has a different look and feel compared to a puffer jacket made with nylon.
• Sustainability: Are eco-friendly materials a priority? Many consumers today prefer sustainable fabrics like organic cotton, recycled polyester, or vegan leather.
• Example: For a jacket designed for outdoor activities, choosing durable, water-resistant fabrics like nylon or Gore-Tex would be ideal, while for a stylish blazer, wool or a wool-blend fabric may be the right choice.
4. Cost and Production Feasibility
The budget for both material sourcing and manufacturing processes must be taken into account. The cost of materials, labour, and production should align with the final selling price.
• Considerations:
• Material Costs: Luxury materials like leather and wool are more expensive, while synthetic fabrics like polyester or nylon are more affordable.
• Production Costs: The complexity of the design (e.g., detailed embroidery, custom zippers) can increase production costs.
• Mass Production vs. Customisation: Are you designing jackets for mass production or bespoke, custom pieces?
• Example: A mass-produced windbreaker for a sporting brand will need to be made from affordable materials and produced efficiently, while a luxury designer leather jacket can justify higher production costs due to its premium materials and craftsmanship.
5. Fashion Trends and Seasons
Jackets, like any other garment, are influenced by fashion trends and the seasons. Understanding current trends and forecasting future ones can help make the design more appealing and marketable.
• Considerations:
• What colours, styles, and materials are trending in the fashion industry?
• Are there any cultural or seasonal factors influencing jacket trends?
• How will your design stand out from competitors while still staying in line with trends?
• Example: The popularity of oversized jackets or techwear styles might influence design choices, while eco-conscious consumers may prefer jackets made with sustainable fabrics.
6. Sustainability and Ethical Manufacturing
With the growing emphasis on sustainable fashion, incorporating eco-friendly practices into the design and production of jackets can significantly enhance the brand’s reputation and appeal.
• Considerations:
• Use of organic or recycled fabrics (e.g., recycled polyester, organic cotton).
• Ethical sourcing and fair labour practices.
• Minimising waste in production (e.g., reducing fabric offcuts).
• Example: Brands like Patagonia have set a standard in producing jackets with sustainable materials and ethical production practices, which resonate with environmentally conscious consumers.
6 Types of Jackets to Add to Your Brand
The jacket manufacturing industry covers a wide range of styles, each suited for different purposes, climates, and audiences. Understanding these categories can help when planning a jacket line or selecting the type of jacket to produce based on market demands. Here are some of the most popular jacket categories:
1. Bomber Jackets
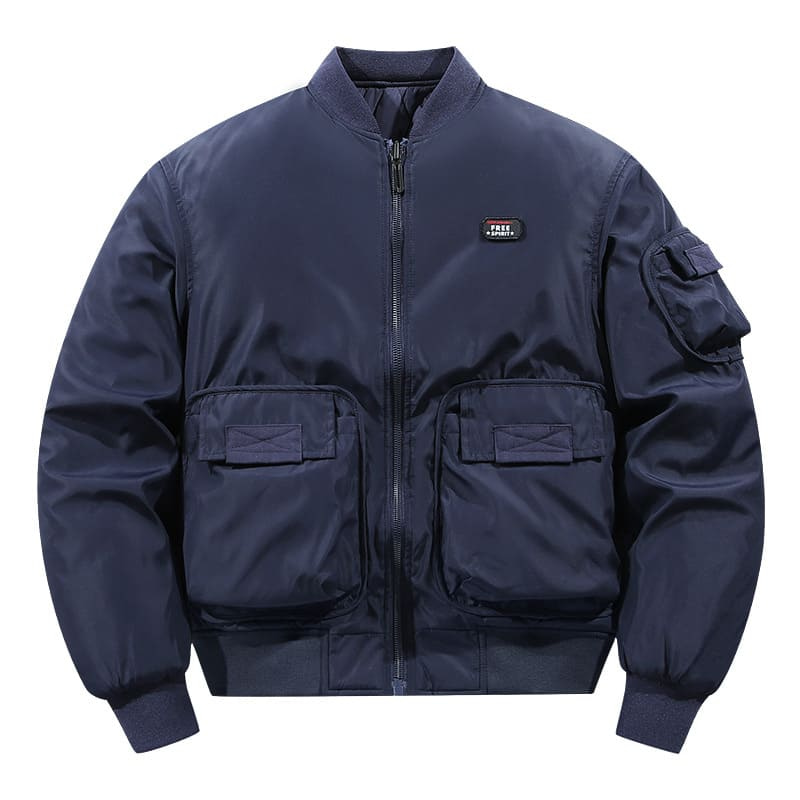
Bomber jackets originated as functional outerwear for military pilots, designed to keep them warm at high altitudes. Today, they’re popular for their casual yet stylish look.
• Materials: Often made from materials like nylon or polyester for a lightweight feel, but leather or wool versions are also common.
• Features: Ribbed cuffs and hems, zip-up fronts, and spacious sleeves for mobility.
• Usage: Bomber jackets suit both casual and semi-formal occasions, appealing to a wide audience.
2. Parkas
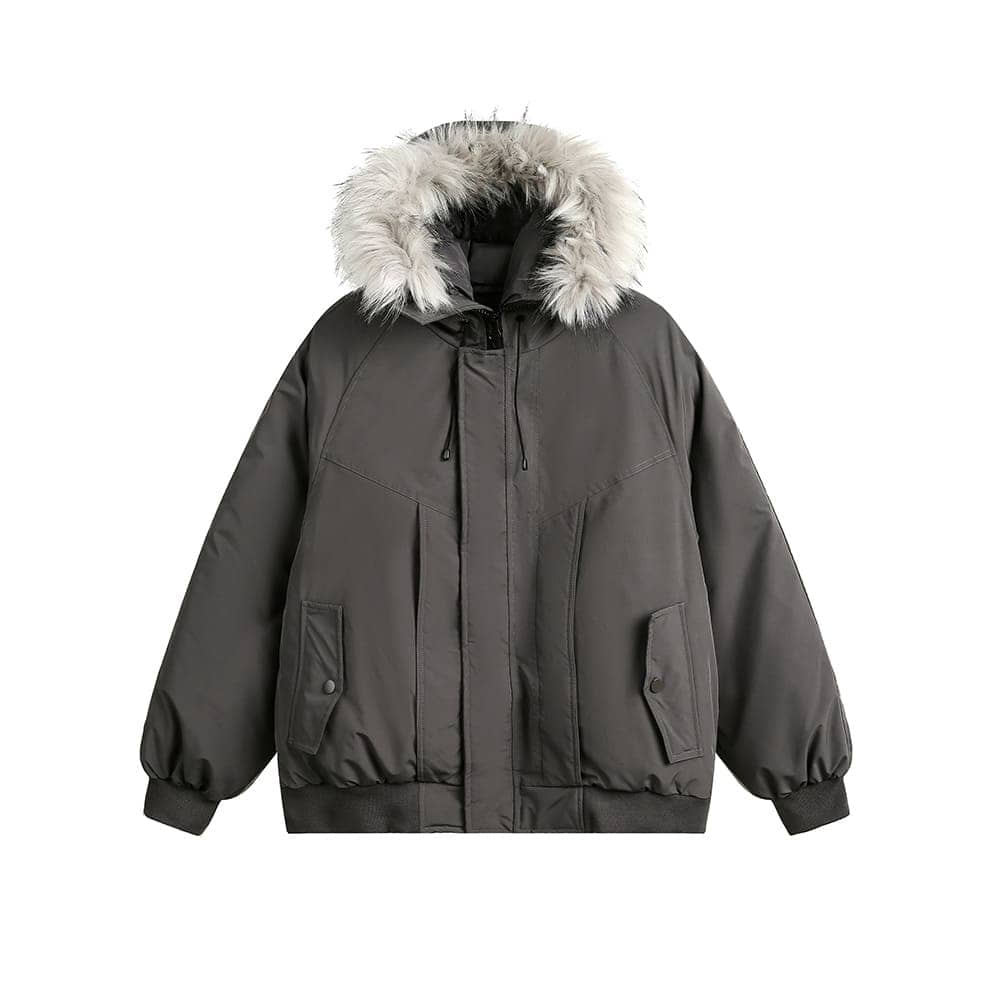
Parkas are designed for warmth, making them ideal for colder climates. They’re often longer, covering the waist and hips for extra protection.
• Materials: Commonly made with insulated layers, such as down or synthetic fills, with waterproof or water-resistant shells.
• Features: Hooded design (sometimes with fur trim), multiple pockets, and zippers with flap coverings for added warmth.
• Usage: Primarily winter wear, parkas are used in urban settings as well as outdoor and adventure wear.
3. Blazers and Suit Jackets
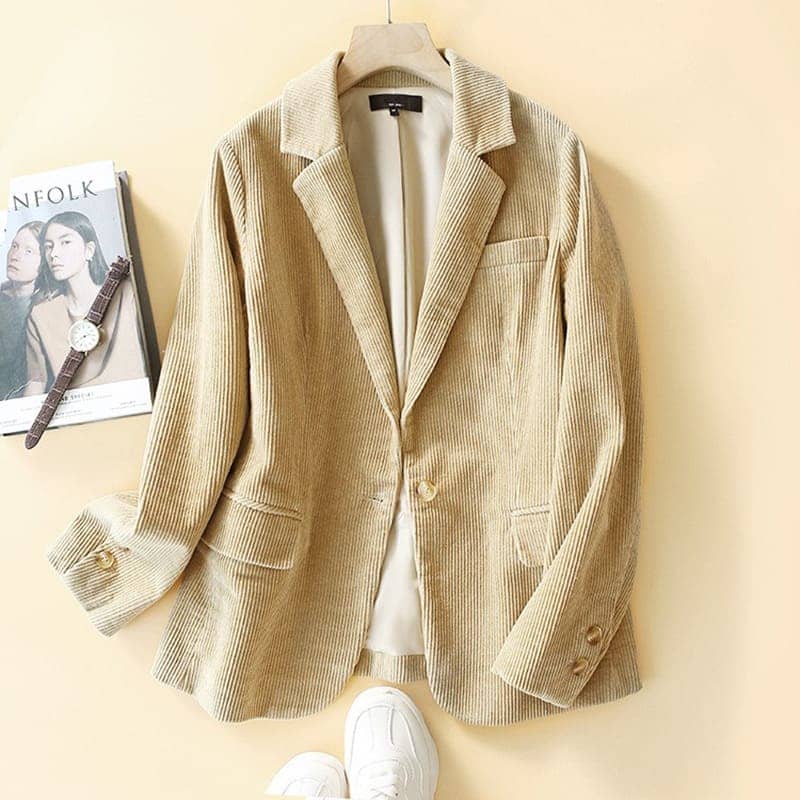
Blazers and suit jackets provide a formal look and are structured for a tailored fit. They’re often part of business attire or smart-casual wardrobes.
• Materials: Wool, wool blends, linen, and polyester are common for their durability and draping qualities.
• Features: Structured shoulders, buttons on the cuffs, and lapels.
• Usage: Ideal for professional or formal settings, but increasingly styled for smart-casual occasions as well.
4. Denim Jackets
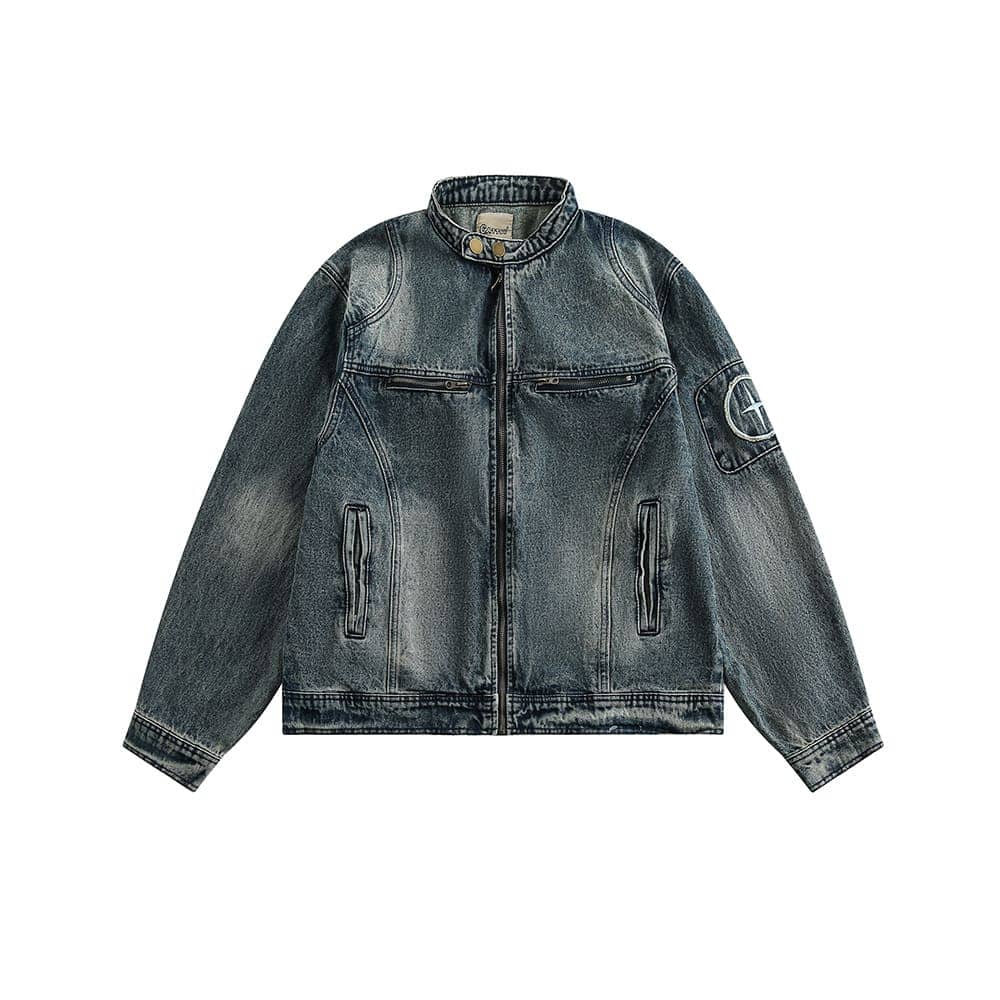
A classic casual style, denim jackets are durable and versatile, suitable for mild weather.
• Materials: Made from heavy cotton denim, which can come in various washes and colours.
• Features: Button-down fronts, chest and side pockets, and often a slim fit.
• Usage: Known for being highly versatile, denim jackets work across seasons and fashion styles, from casual to semi-formal.
5. Leather Jackets
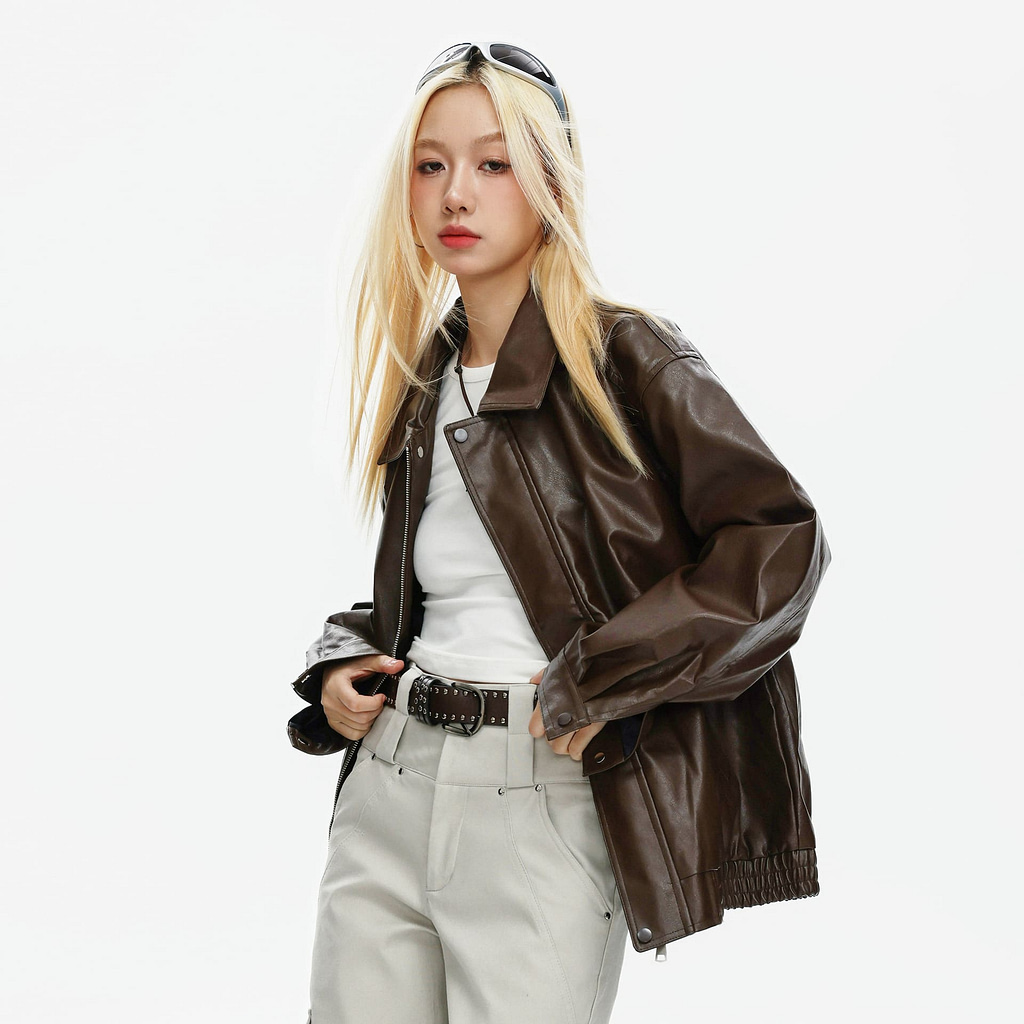
Leather jackets are iconic, known for their edgy, stylish look.
• Materials: Genuine leather, faux leather, or vegan leather options, with a variety of finishes (e.g., glossy, matte).
• Features: Often fitted with zippers, studs, or other embellishments.
• Usage: Primarily casual and streetwear, though leather blazers are used in smart-casual wardrobes.
6. Windbreakers and Rain Jackets
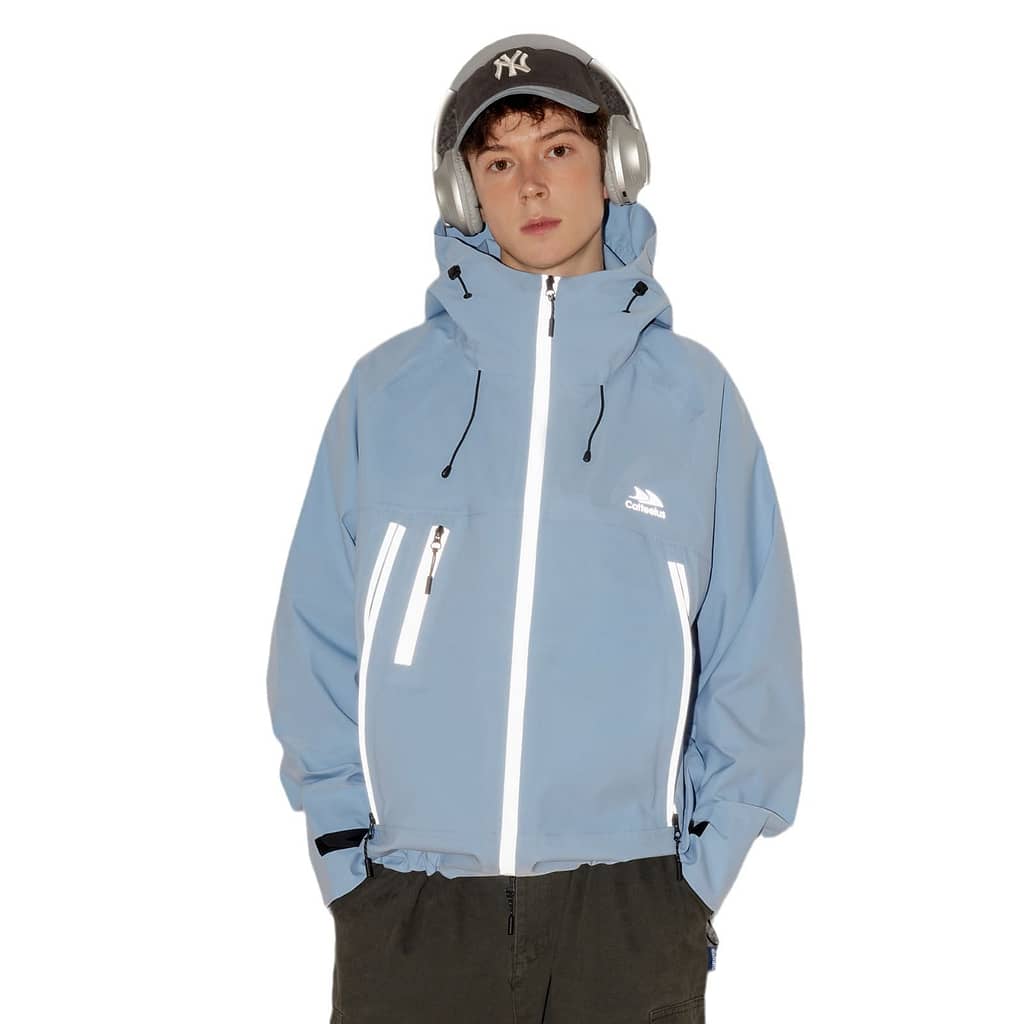
Lightweight and water-resistant, windbreakers and rain jackets are perfect for unpredictable weather.
• Materials: Nylon or polyester with water-resistant or waterproof coatings.
• Features: Hoods, zip-up fronts, elastic cuffs, and sometimes ventilation for breathability.
• Usage: Outdoor activities, sports, or commuting, offering protection from wind and rain without the bulk.
Fabrics Suitable for Making Jackets
Choosing the right fabric is critical to jacket manufacturing, as it affects not only the jacket’s appearance but also its durability, insulation, and comfort. Here are some of the most popular fabrics used in jacket production:
1. Cotton and Cotton Blends
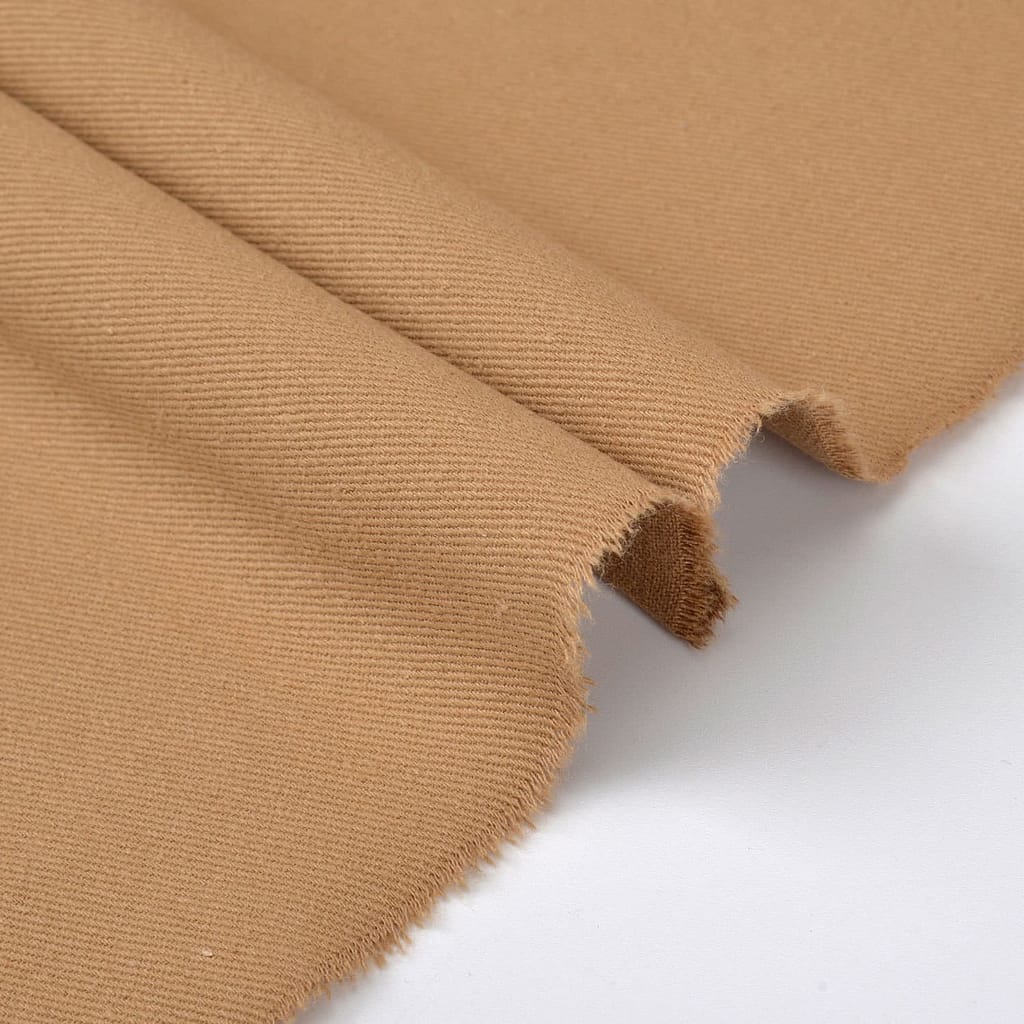
Cotton is a versatile, breathable fabric, making it ideal for lightweight and casual jackets. Cotton blends add more durability or weather resistance by mixing with materials like polyester.
• Benefits: Comfortable, breathable, soft on the skin, and easily dyed.
• Drawbacks: Cotton alone isn’t very water-resistant, so it’s not ideal for jackets meant for wet or cold conditions.
• Common Uses: Trench coats, lightweight blazers, and casual jackets.
2. Wool and Wool Blends
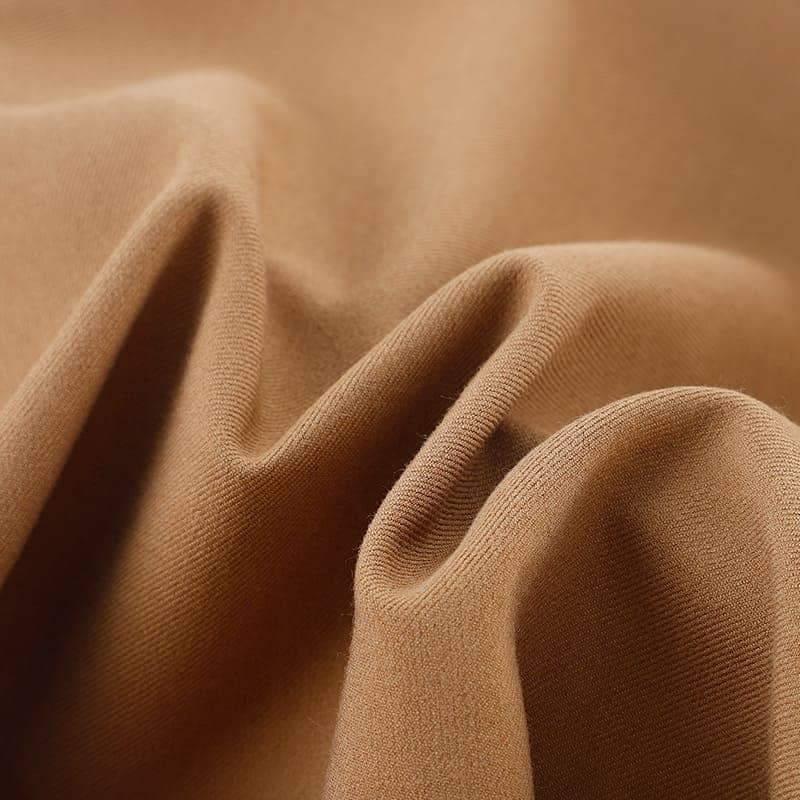
Wool is excellent for insulation, making it suitable for jackets designed for colder weather. Wool blends, which may include synthetic fibres, are used to make the fabric more durable and less prone to shrinking.
• Benefits: Warm, durable, and can be woven to different textures and thicknesses.
• Drawbacks: Wool is generally heavier and can be less breathable.
• Common Uses: Peacoats, blazers, and winter coats.
3. Leather and Faux Leather
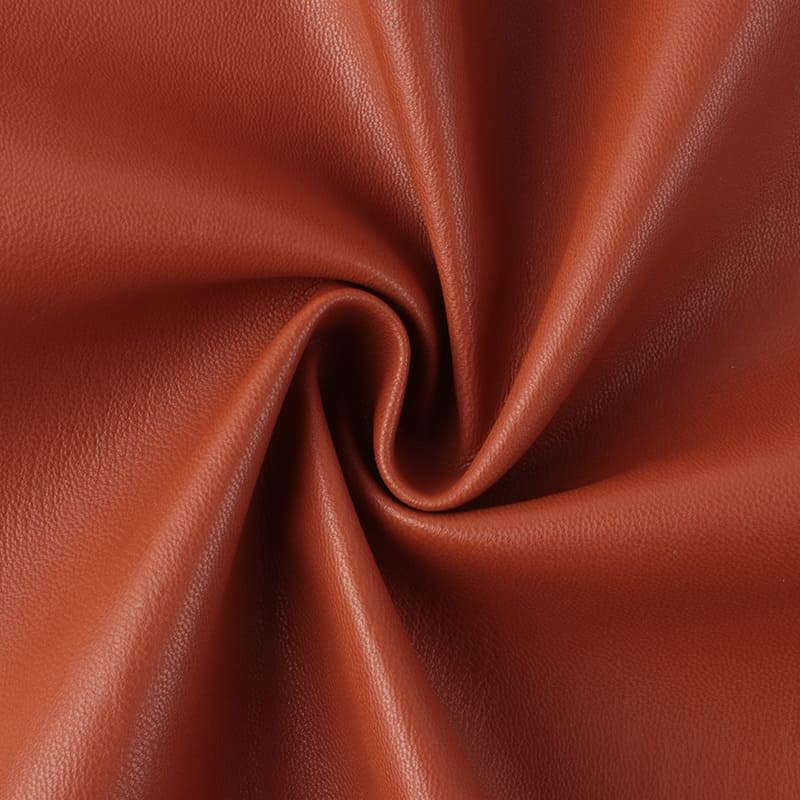
Leather offers durability and a stylish look, often associated with premium quality and an edgy aesthetic. Faux leather provides a similar look and feel without using animal products.
• Benefits: Leather is durable, wind-resistant, and has a unique appearance; faux leather is more affordable and vegan-friendly.
• Drawbacks: Leather requires special care, and genuine leather can be expensive.
• Common Uses: Bomber jackets, biker jackets, and fashion-forward designs.
4. Denim
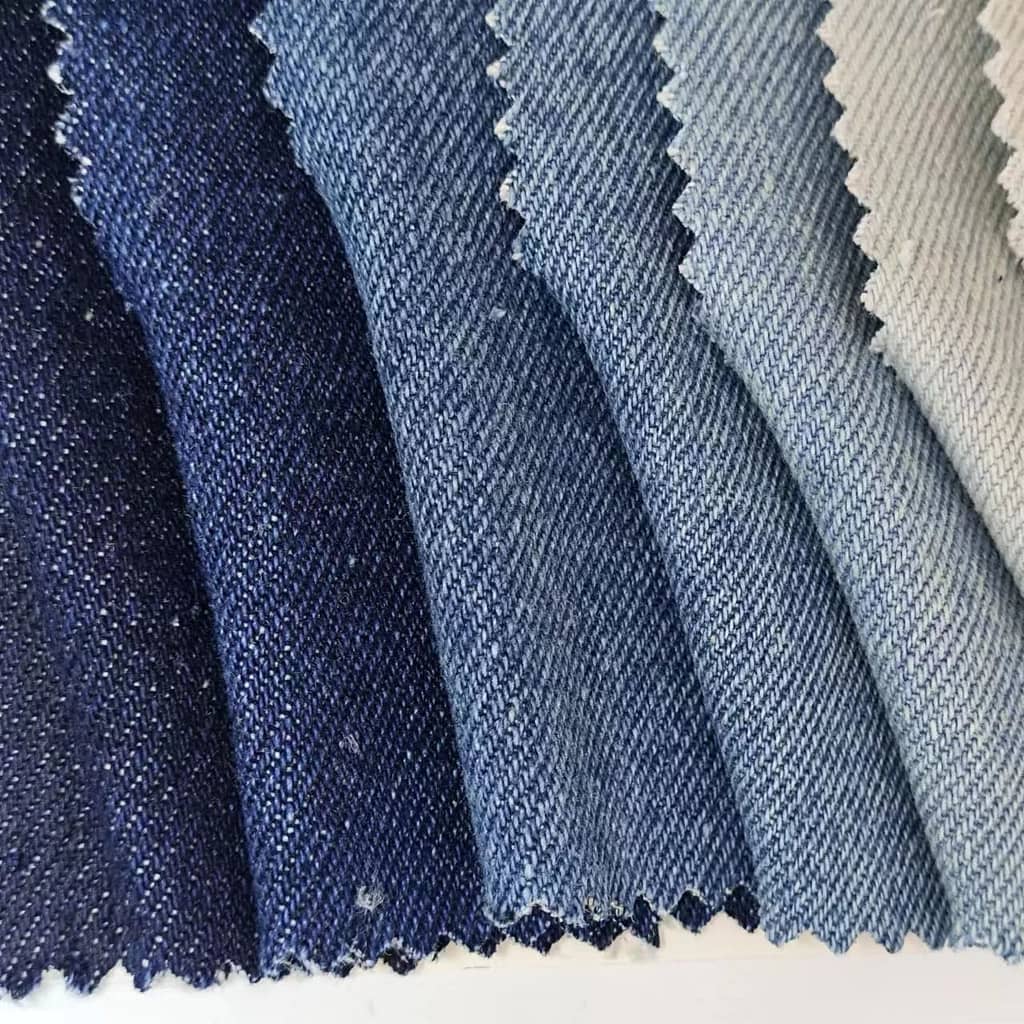
Denim, made from cotton, is a rugged and durable fabric, ideal for jackets that see everyday wear. It’s known for its characteristic texture and resistance to wear and tear.
• Benefits: Long-lasting, breathable, and available in a variety of colours and washes.
• Drawbacks: Denim doesn’t offer much insulation and is best for mild weather.
• Common Uses: Casual jackets and workwear-inspired designs.
5. Nylon and Polyester

Nylon and polyester are popular synthetic fabrics known for their lightweight and weather-resistant qualities.
• Benefits: Water-resistant, durable, quick-drying, and available in various weights.
• Drawbacks: Can feel less breathable than natural fibres and may lack the aesthetic appeal of materials like leather.
• Common Uses: Windbreakers, rain jackets, and sports jackets.
6. Insulation Materials
Insulation materials are often added as inner layers for jackets intended for colder weather, providing warmth without excessive weight.
• Down: Made from the soft under-feathers of ducks or geese, down is lightweight, compressible, and provides excellent insulation.
• Synthetic Insulation: Made from polyester fibres, synthetic insulation mimics down but performs better in wet conditions, as it retains warmth even when damp.
• Fleece and Thermal Fabrics: These materials are used as lining to add warmth, especially in jackets for winter or cold climates.
7. Specialty Fabrics (e.g., Gore-Tex, Fleece)
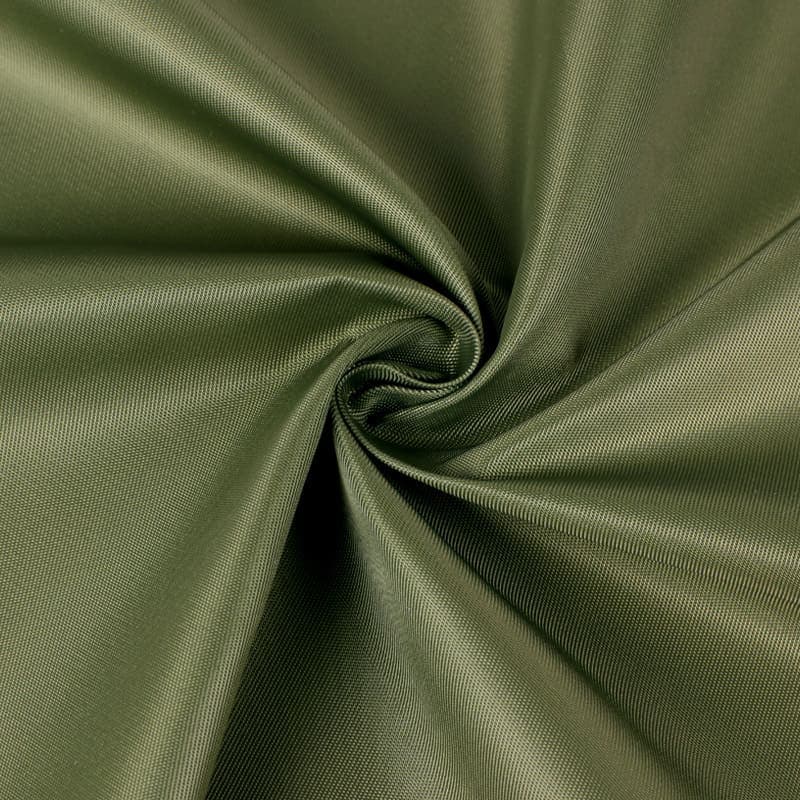
Specialty fabrics are often used for jackets intended for specific outdoor conditions. For example, Gore-Tex is both waterproof and breathable, making it popular for high-performance outdoor jackets.
• Benefits: Designed for extreme conditions, usually durable and resistant to the elements.
• Drawbacks: Higher cost, with limited use outside of specific performance needs.
• Common Uses: Outdoor jackets, rainwear, and ski jackets.
How Do the Jacket Manufacturers Make Patterns?
Jacket manufacturers use a detailed and precise process to create patterns for jacket production. Here’s an overview of how they typically make patterns:
Initial Design and Sketching
The process begins with the designer creating a sketch or technical drawing of the jacket. This initial design outlines the basic shape, style, and features of the jacket.
Pattern Development
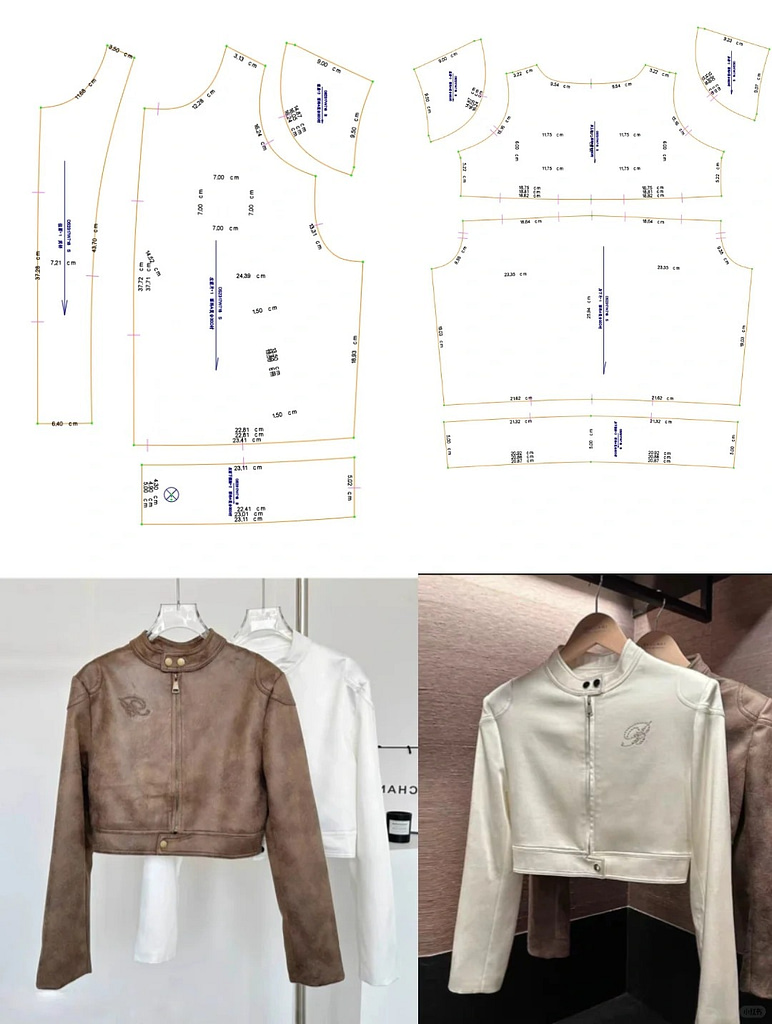
Basic Block Creation
Pattern makers start with a basic jacket block, which is a standard template that represents the fundamental shape of a jacket. This block is based on average body measurements for the target market.
Pattern Modification
The basic block is then modified to match the specific design of the jacket:
- Adjusting the silhouette
- Adding design features like pockets, lapels, and collars
- Modifying sleeve shape and length
- Incorporating any unique style elements
Separate Pattern Pieces
For a typical jacket, multiple pattern pieces are created, including:
- Front panels
- Back panels
- Sleeves
- Collar
- Lapels
- Pockets
- Lining pieces
- Interfacing pieces
Technical Specifications
The pattern includes technical details such as:
- Seam allowances (typically 1 cm for jackets)
- Notches for aligning pieces
- Grain lines
- Buttonhole and button placement
- Dart positions
Pattern Grading
Once the base pattern is finalized, it is graded to create patterns for different sizes. This involves systematically adjusting the pattern pieces to accommodate various body measurements.
Digital Pattern Making
Many manufacturers now use Computer-Aided Design (CAD) software for pattern making. This allows for:
- Greater precision
- Easier modifications
- Digital storage and sharing of patterns
- Integration with automated cutting systems
Pattern Testing and Refinement
Sample Creation
A prototype jacket is made using the pattern to test fit and construction.
Fit Testing
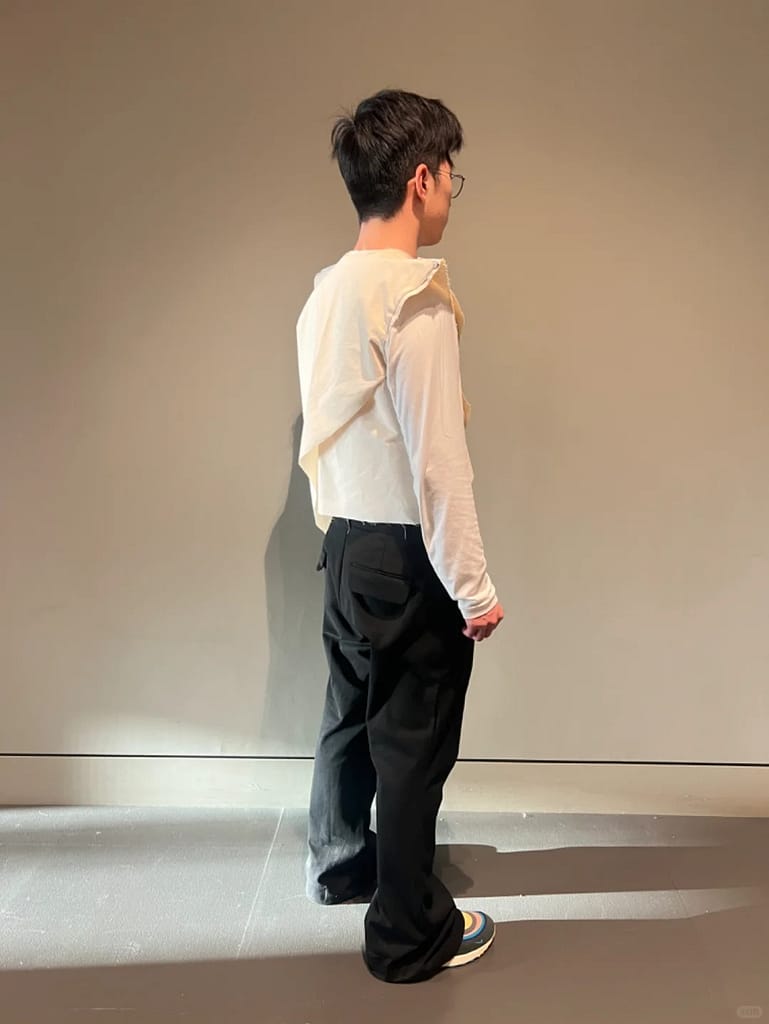
The sample is evaluated on a fit model or dress form to assess:
- Overall fit and comfort
- Proper alignment of seams and design features
- Aesthetic appearance
Pattern Refinement
Based on the fit test results, the pattern is adjusted and refined as needed.
Production Pattern Finalization
Once all adjustments are made, the final production pattern is created. This includes:
- All necessary markings for production
- Detailed instructions for assembly
- Specifications for materials and notions
By following this meticulous process, jacket manufacturers ensure that their patterns will produce well-fitting, high-quality jackets that meet design specifications and can be consistently reproduced in various sizes.
How Do Jacket Manufacturers Cut and Sew the Fabric?
Jacket manufacturers use a sophisticated process to cut and sew fabric, combining traditional techniques with modern technology. Here’s an overview of how they typically approach this:
Cutting Process
Pattern Creation and Grading
The process begins with creating the jacket pattern, usually using computer-aided design (CAD) software. The base pattern is then graded to produce patterns for different sizes.
Fabric Layering
Large cutting tables are used to spread multiple layers of fabric. The number of layers depends on the fabric type and cutting method.
Marker Making
A marker, which is the layout of pattern pieces on the fabric, is created to maximize fabric utilization. This is often done using specialized software.
Cutting Methods
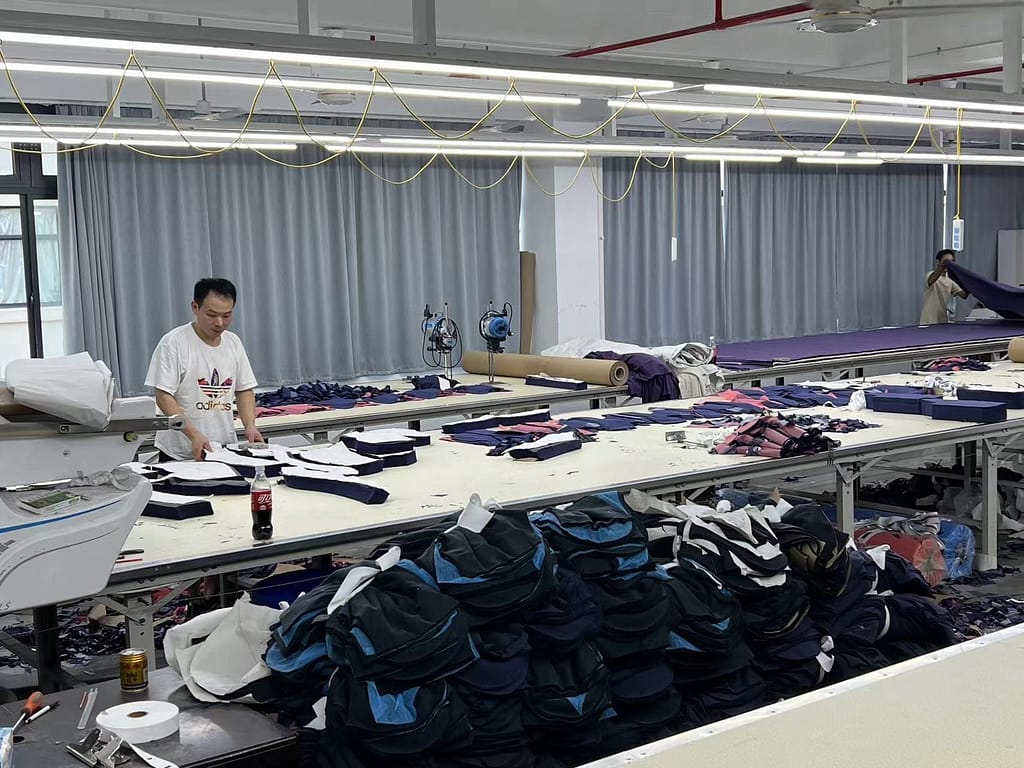
Manufacturers use various cutting methods, depending on their scale and technology:
- Manual cutting: Skilled workers use tools like scissors or electric cutters for small batches or delicate fabrics.
- Semi-automated cutting: Electric cutting machines are guided by operators around pattern outlines.
- Automated cutting: Computer-controlled machines, such as those made by Gerber Garment Technology, use vacuum technology to hold fabric in place while cutting with high precision and speed.
Sewing Process
Component Preparation
Cut pieces are sorted, bundled, and labeled by size and component to avoid confusion in later stages.
Assembly Line Setup
The sewing process is typically divided into sections:
- Body fabric sewing
- Lining sewing
- Sleeve sewing
- Canvas sewing (for structured jackets)
- Final assembly
Specialized Machines
Jacket production requires various specialized sewing machines, including:
- Automatic pocket-attaching machines
- Automatic belt-loop attaching machines (for certain styles)
- Machines with automated bobbin changers
Key Sewing Processes
Some crucial sewing processes for jackets include:
- Sleeve cuff stitching
- Pocket creation
- Shoulder seam construction
- Front zipper installation
- Collar attachment
- Lining integration
Quality Control
Throughout the sewing process, quality checks are performed to ensure accuracy and consistency.
Finishing
After sewing, jackets undergo finishing processes:
- Thread trimming
- Pressing using specialized equipment (e.g., body pressing machines, sleeve pressing machines)
- Button attachment
- Final inspection and tagging
By combining these cutting and sewing techniques, jacket manufacturers can efficiently produce high-quality garments while maintaining consistency across different sizes and styles.
The Printing Techniques in the Jacket Manufacturing Industry
Jacket manufacturers employ several printing techniques to add designs, patterns, and branding to their products. Here are some of the most common printing methods used in jacket manufacturing:
Screen Printing
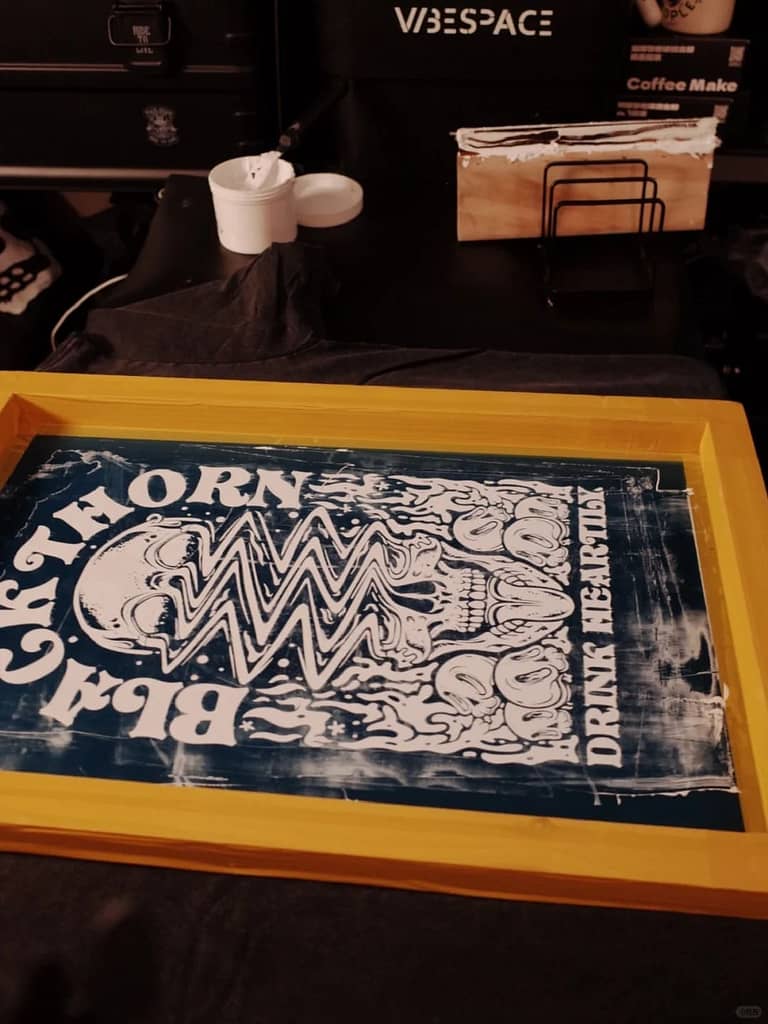
Screen printing is one of the most popular methods for printing on jackets, especially for designs with bold colors and logos.
- Suitable for: T-shirts, sweatshirts, and jackets
- Advantages:
- Cost-effective for large orders
- High color vibrancy and durability
- Works well for both simple and complex designs
- Disadvantages:
- High setup costs for multiple colors
- Not ideal for small production runs
Heat Transfer Printing
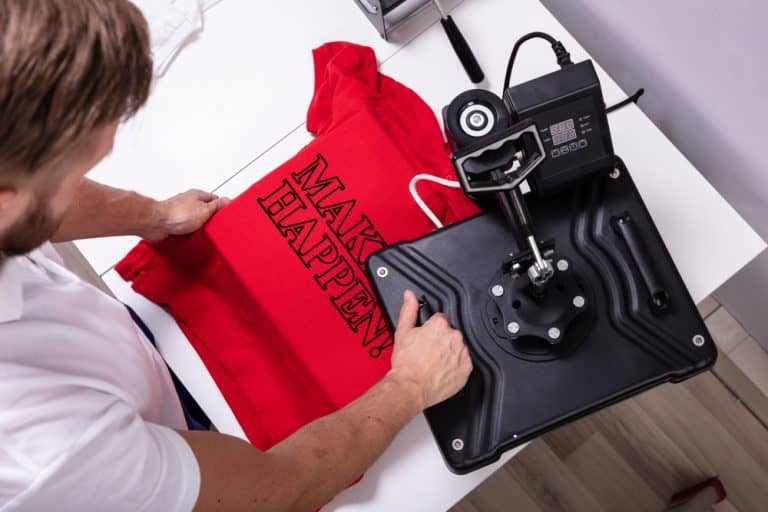
This method involves printing designs onto transfer paper and then applying heat to transfer the design onto the jacket fabric.
- Suitable for: Various personalized clothing items, including jackets
- Advantages:
- Ideal for low to medium production runs
- Suitable for complex designs and full-color prints
- Quick turnaround time
- Disadvantages:
- Prints may crack or fade over time
- Not as durable as some other methods
Direct-to-Garment (DTG) Printing
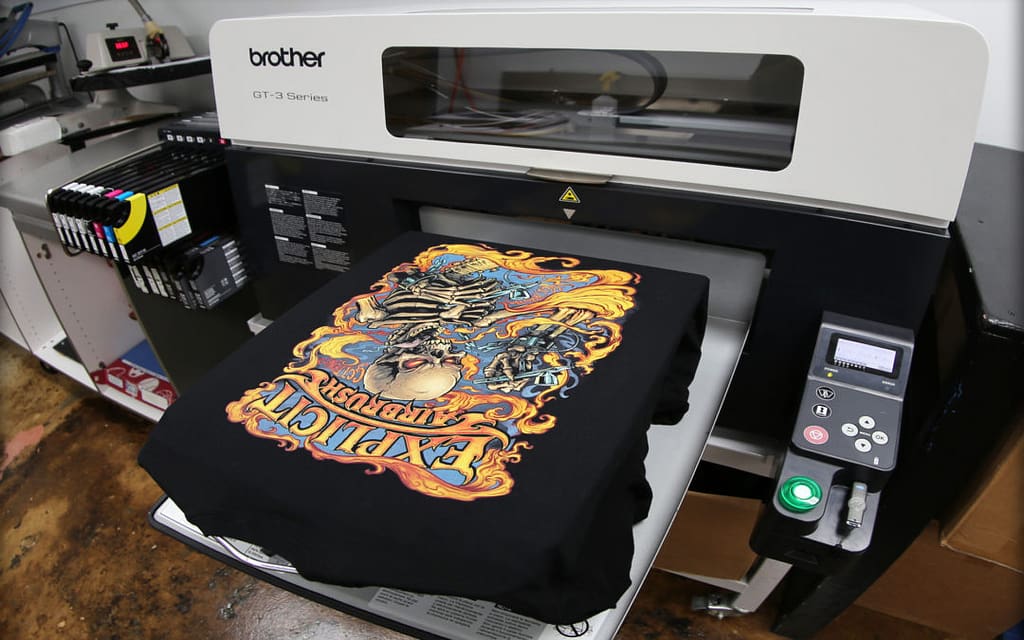
DTG printing involves digitally printing designs directly onto the jacket fabric using specialized inkjet printers.
- Suitable for: Custom jackets with detailed designs
- Advantages:
- Low setup costs, ideal for small runs
- High color vibrancy and detail
- Quick turnaround time
- Disadvantages:
- Cost per unit can be high for larger orders
- Limited to certain fabric types
Sublimation Printing
This technique uses heat to transfer dyes onto the fabric, creating vibrant and durable prints.
- Suitable for: Sportswear, outdoor apparel, and jackets made from synthetic materials
- Advantages:
- High color vibrancy and durability
- Excellent for all-over prints
- Ideal for synthetic fabrics like polyester
- Disadvantages:
- Not suitable for natural fibers like cotton
- Requires specific equipment and materials
Embroidery
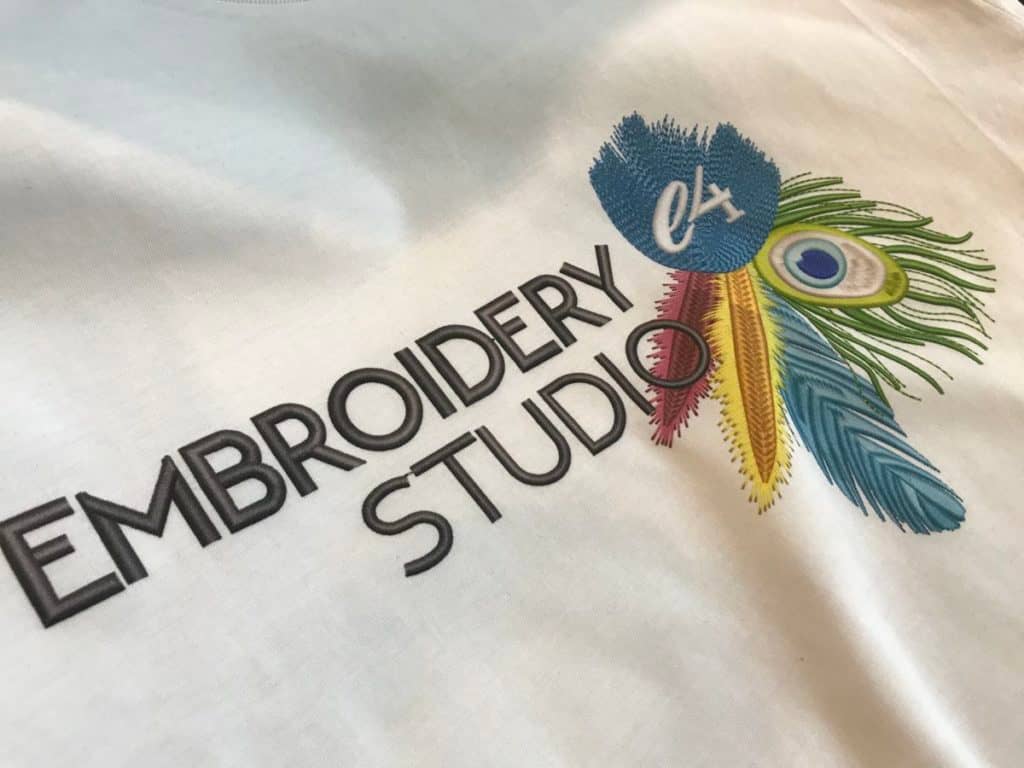
While not strictly a printing method, embroidery is often used on jackets for logos and small designs.
- Advantages:
- Adds texture and sophistication
- Durable and long-lasting
- Works well for logos and small designs
When choosing a printing method for jackets, manufacturers consider factors such as the fabric type, design complexity, production volume, and desired aesthetic. Often, a combination of these techniques may be used to achieve the desired result on different parts of the jacket.
Summarize the Jacket Manufacturing Process
Manufacturing a jacket involves several stages, each of which plays a vital role in ensuring the jacket is well-made, durable, and market-ready. The process can vary depending on the complexity of the design and the materials used, but here’s an overview of the typical jacket manufacturing workflow:
1. Design and Prototyping
The first stage in jacket manufacturing is design. This is where ideas and sketches are translated into functional designs, and prototypes are created.
• Step Details:
• The design team works with pattern makers to create technical drawings of the jacket, specifying measurements, fabric choices, stitching details, and features (such as pockets, zippers, or hoods).
• A prototype (a sample version of the jacket) is then created. This is essential for testing the design, fit, and functionality of the jacket.
• Adjustments are made based on feedback from the sample, and another prototype may be produced if necessary.
• Example: For a new line of winter jackets, designers will experiment with different insulation materials and test the overall fit to ensure comfort and warmth before proceeding.
2. Fabric Sourcing and Cutting
Once the prototype is approved, the next step is to source the fabrics and cut them into the required shapes based on the patterns.
• Step Details:
• Materials are sourced from fabric suppliers, who provide the necessary quantities of the chosen fabrics (such as wool, nylon, or cotton blends).
• The fabrics are then cut using industrial machines based on the jacket’s patterns. Modern factories use laser cutting or automated cutting machines for precise and efficient cutting of the fabric pieces.
• The cutting stage also involves marking the fabric to ensure the pieces are correctly aligned for stitching.
• Example: A manufacturer sourcing high-quality leather will need to ensure that it’s properly inspected for imperfections before cutting, as leather is a premium material with natural variations.
3. Sewing and Assembly
After the fabric pieces are cut, they are sent to the sewing department, where they are stitched together to form the jacket.
• Step Details:
• Skilled workers use industrial sewing machines to assemble the pieces of fabric. This process includes attaching sleeves, zippers, lining, and other elements like cuffs and collars.
• For jackets with complex designs, such as quilted or padded jackets, additional steps like adding insulation or lining are done during this stage.
• Double stitching or reinforcement stitching may be used to ensure durability, especially for high-stress areas like the shoulders or pockets.
• Example: For a waterproof jacket, the sewing process must include ensuring the seams are sealed properly to prevent water from leaking through, often using heat bonding or taping.
4. Fitting and Quality Control
Once the jacket is assembled, it’s time for fitting and quality control checks. This step ensures the jacket fits correctly, is functional, and meets the required standards.
• Step Details:
• Jackets are tried on models (or mannequins) to check for proper fit and sizing. Adjustments may be made to ensure the jacket fits a range of body types, especially for mass-market products.
• Quality control inspectors carefully examine each jacket for defects, such as stitching errors, fabric flaws, or missing components.
• The jacket is also tested for performance – for example, checking zippers, adjusting closures, or testing waterproof features.
• Example: A quality control inspector may perform a water test on a rain jacket to ensure it remains dry even after prolonged exposure to water.
5. Finishing Touches
Once the jacket passes quality control, the final steps are completed, including adding any last-minute details that enhance the jacket’s appearance or functionality.
• Step Details:
• Labels and branding are attached, including the care label, brand logo, and size tags.
• Additional features like drawstrings, buttons, or embellishments are added at this stage.
• The jackets are pressed or steamed to remove any wrinkles that may have occurred during the manufacturing process.
• Example: For a designer jacket, a logo might be embroidered on the sleeve, while for a functional outdoor jacket, reflective strips might be added for safety.
6. Packing and Shipping
Once all finishing touches are complete, the jackets are packed and prepared for shipping.
• Step Details:
• Jackets are folded or hung on hangers, depending on the design and fabric. Care is taken to ensure the jackets are not damaged in transit.
• The jackets are then packaged with protective materials like plastic covers or garment bags to prevent dirt and moisture from affecting the finished product.
• The final jackets are grouped and shipped to retail stores, distribution centres, or directly to customers if sold online.
• Example: A batch of jackets for retail stores may be packed in bulk cartons, while online orders may involve individual packaging with personalised thank-you notes or branded tags.
In Conclusion
Creating a successful jacket brand demands a blend of creativity, industry expertise, and careful attention to every detail. By collaborating with skilled jacket manufacturers, you gain access to their experience and resources, making it easier to turn your vision into reality.
Building a brand takes dedication and persistence, but with the right guidance and support, you can craft a jacket collection that connects with your target audience and shines in the competitive fashion market.
We’re here to provide the expertise and assistance you need every step of the way. Reach out to Valtin Apparel today, and let’s work together to bring your brand to life!
FAQs:
1. What are the best fabrics for cold-weather jackets?
For cold-weather jackets, wool, down, synthetic insulation, and Gore-Tex are excellent choices. Wool and down offer great warmth, while synthetic insulation works well for both warmth and moisture resistance.
2. How can I make sure my jacket is waterproof?
To make your jacket waterproof, use waterproof fabrics like Gore-Tex, and ensure the seams are sealed using bonding or taping. Water-resistant zippers and pockets also help keep moisture out.
3. How do I choose the right material for a jacket?
Consider the jacket’s intended use. Lightweight materials like cotton or polyester are good for casual wear, while weather-resistant materials like nylon, Gore-Tex, or leather are ideal for outdoor jackets.
4. Can jackets be custom-designed?
Yes, jackets can be custom-designed with unique fabrics, features, and finishes. Many manufacturers offer bespoke services for premium or limited-edition jackets.