Knitwear is a must-have item for autumn and winter, and many clothing brands launch it as an important product line. However, the production of knitwear is different. Generally speaking, clothing is completed by cutting the fabric and then sewing it together. Knitwear is made by machines that spin the yarn into the pieces of fabric needed to make the clothes and then sew them together to make the garment. This leads to many clothing startups who are planning to launch a knitwear product line not knowing how to design the styles and having communication barriers with the factory.
So today’s article will introduce you to the process of knitwear manufacturing through the simplest content. If you have any questions during the reading, you can also contact us at any time, and we are willing to provide you with detailed answers. So let’s start.
Before Knitwear Production: From Yarn to Design
Knitwear manufacturing starts with two fundamental steps: the selection of yarn materials and the design of the garment. These decisions define the final product’s quality, durability, and appeal. Let’s explore the yarn compositions commonly found in the market and their impact on knitwear production.
Selecting Yarn Materials
Choosing the right yarn is crucial for determining how your knitwear will feel, perform, and look. Different yarn compositions offer varying levels of softness, warmth, elasticity, and sustainability. Below are the common yarns used in knitwear manufacturing today:
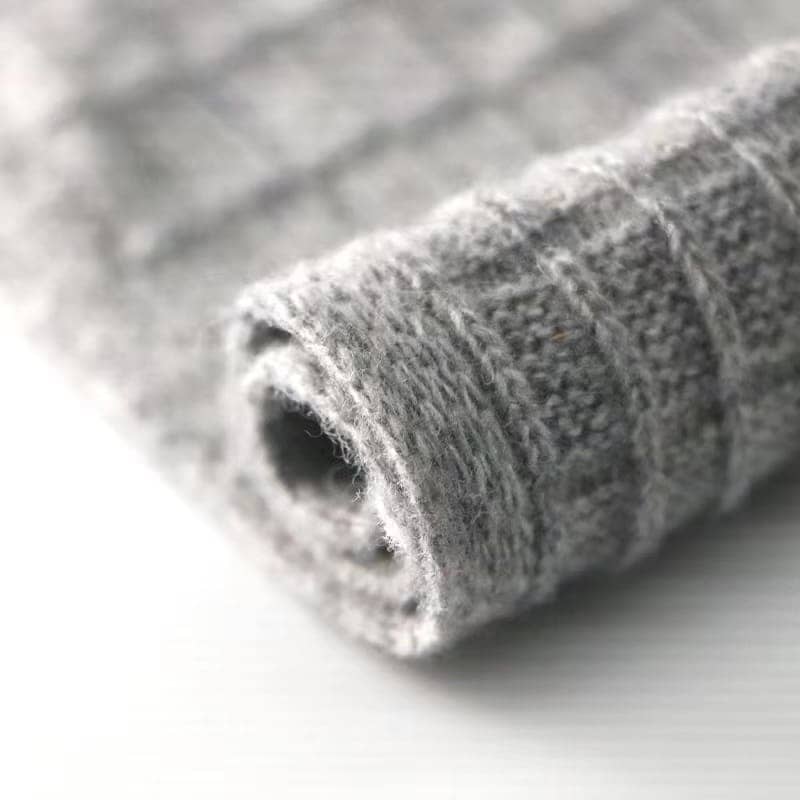
• Wool: One of the most traditional and widely used fibers in knitwear, wool is known for its warmth, breathability, and natural stretch. Wool knitwear is typically soft, insulating, and moisture-wicking, making it ideal for winter garments like sweaters, scarves, and coats. Wool is also highly durable and resistant to wear, though it requires special care when washing to prevent shrinking.
• Wool Blends: To enhance the properties of pure wool or reduce costs, manufacturers often blend wool with other fibers such as polyester, acrylic, or nylon. These blends maintain the warmth and softness of wool but improve durability, elasticity, and resistance to wrinkling or pilling. Wool blends are perfect for mid-priced sweaters and jackets that need to balance warmth with cost-effectiveness.
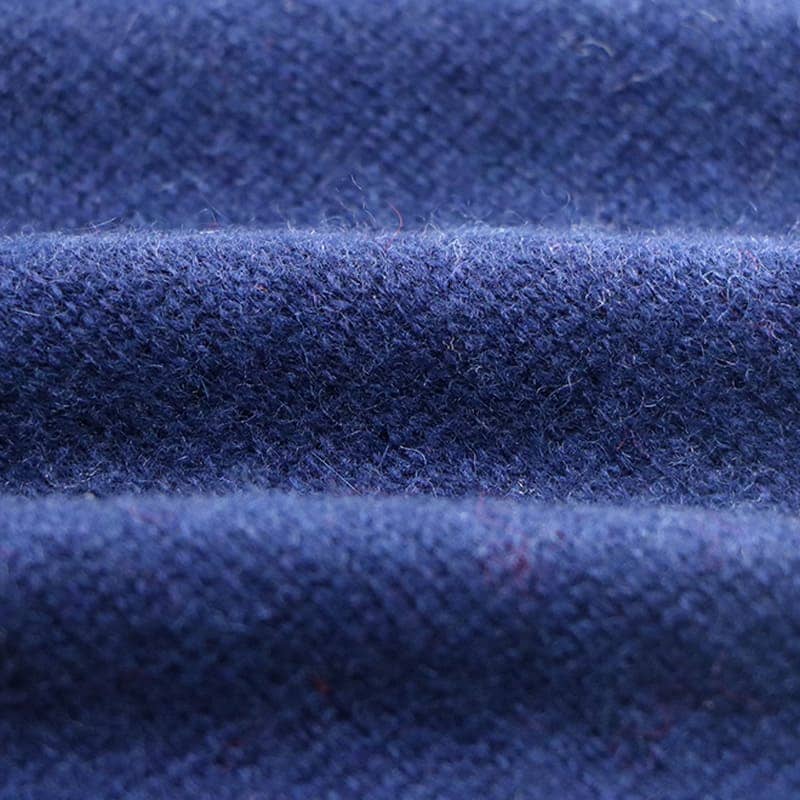
• Cashmere: Prized for its unparalleled softness and luxury, cashmere is a finer, more delicate fiber than wool. It provides exceptional warmth while being incredibly lightweight and soft to the touch. Cashmere knitwear is often used in high-end fashion items like sweaters, scarves, and cardigans. However, due to its delicacy, cashmere requires careful handling and is typically more expensive than other yarns.
• Alpaca: Known for its silky texture and thermal properties, alpaca fiber is lightweight, hypoallergenic, and warmer than wool. It’s a sustainable option as alpacas have a minimal environmental impact. Alpaca is often blended with other fibers like wool or acrylic to create durable and lightweight knitwear, making it ideal for luxury winter garments.
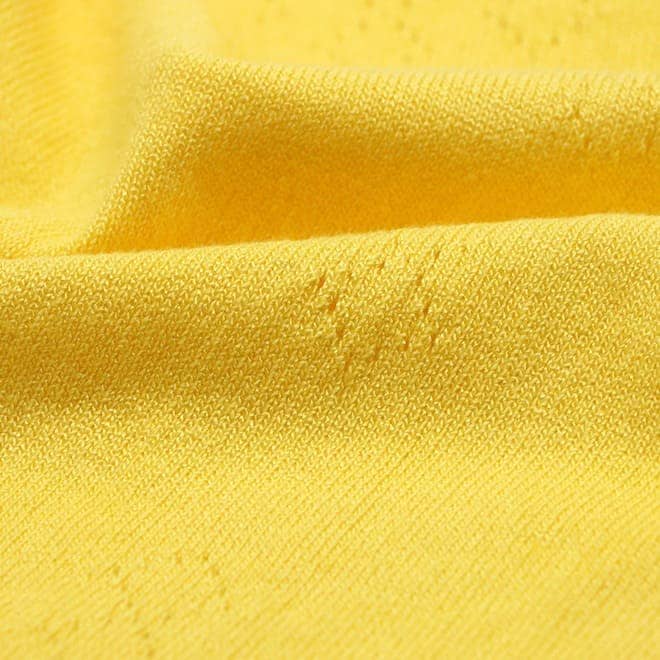
• Viscose: This semi-synthetic fiber is made from wood pulp and mimics the softness and smooth texture of natural fibers like cotton or silk. Viscose is breathable, lightweight, and comfortable, making it a popular choice for both summer and winter knitwear. It is often used in blends to improve the drape and softness of knit garments, especially in fashion-forward pieces.
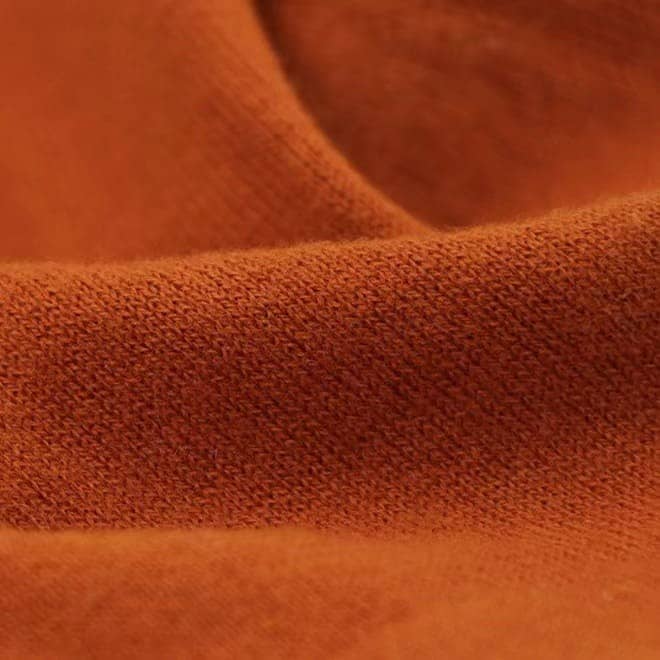
• Pure Cotton: Cotton is highly breathable, soft, and moisture-absorbing, making it perfect for lightweight and comfortable knitwear such as t-shirts, cardigans, and hoodies. Unlike wool, cotton is more suited for warmer seasons or layering, as it provides less insulation. Pure cotton is also sustainable and hypoallergenic, which appeals to eco-conscious brands.
• Cotton and Acrylic Blend: Combining the natural softness and breathability of cotton with the durability and wrinkle-resistance of acrylic, this blend is ideal for everyday knitwear that requires easy care and long-lasting wear.
• Acrylic: Acrylic is a synthetic fiber often used as a cost-effective alternative to wool. It provides warmth and softness, mimicking the texture of wool but at a lower price point. Acrylic knitwear is lightweight and highly durable, making it a practical choice for budget-friendly sweaters and scarves. However, it may lack the breathability of natural fibers and is more prone to pilling over time.
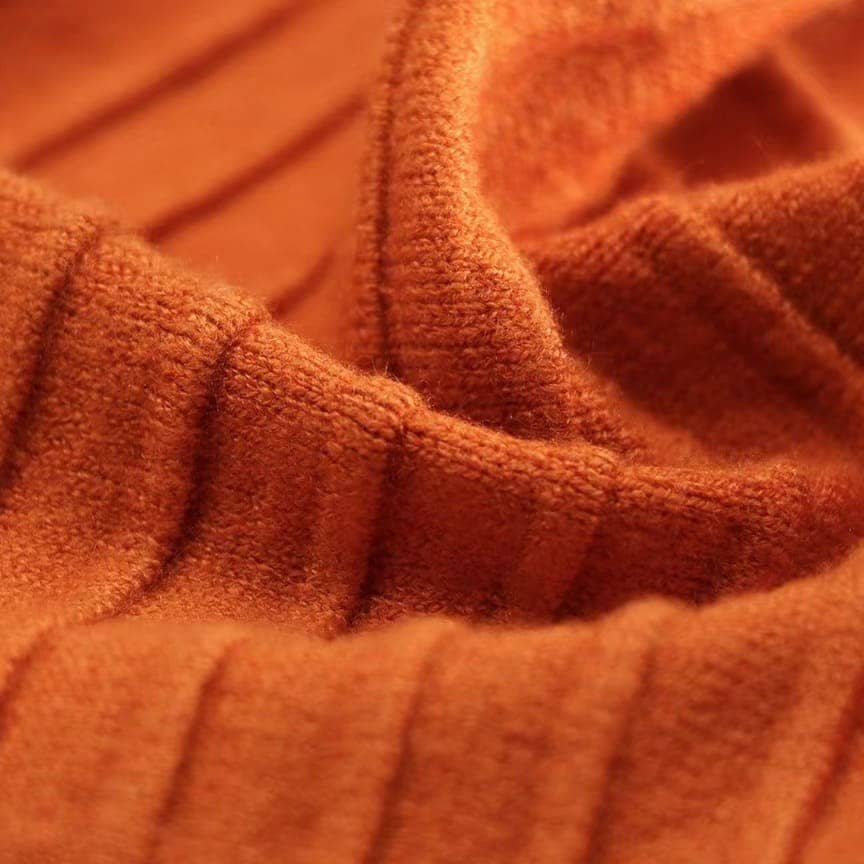
• Core-Spun Yarn (Viscose, Nylon, Polyester Blend): Core-spun yarn is a combination of multiple fibers, usually with a synthetic core (like nylon or polyester) wrapped with a natural or semi-synthetic outer layer (such as viscose). This blend offers the benefits of both durability and softness. Core-spun yarns provide excellent elasticity, making them ideal for knitwear that needs to maintain its shape while offering comfort and stretch, such as fitted tops and knit dresses.
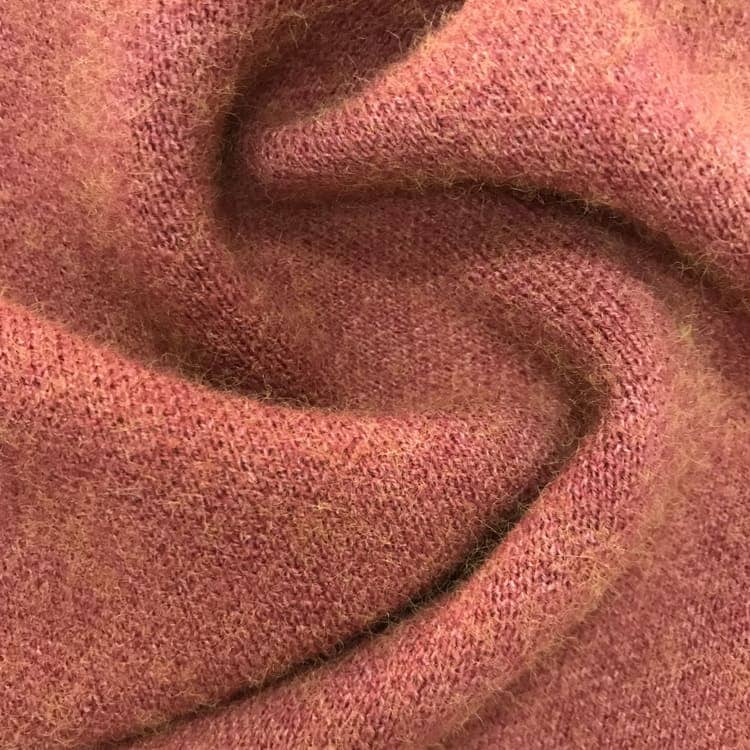
• Acrylic, Viscose, Nylon Blend: This blend combines the best qualities of its constituent fibers. Acrylic provides warmth and softness, viscose adds breathability and a smooth texture, and nylon increases strength and flexibility. Knitwear made from this blend is lightweight, durable, and affordable, making it suitable for both casual and fashion-forward garments.
Each of these yarn compositions offers unique benefits depending on the end use of the garment. B2B buyers should carefully select the right material to match their brand’s needs, whether they’re prioritizing luxury, affordability, or sustainability.
Designing Knitwear
After selecting the appropriate yarn, the next step is designing the knitwear. Knitwear design involves balancing aesthetic appeal with functionality to ensure the final product meets consumer expectations. Key elements to consider in the design phase include:
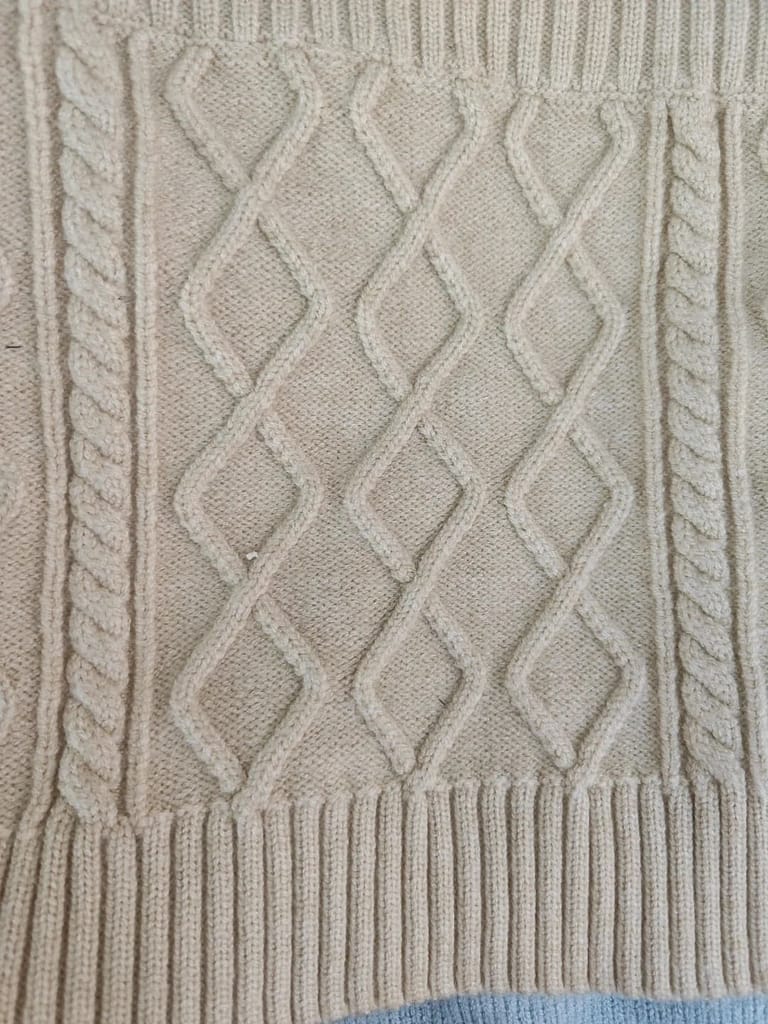
• Stitch Patterns: Various stitch patterns, such as ribbing, cables, and jacquard, create different textures and effects on the surface of the knitwear. These patterns can add complexity to the design, enhance the garment’s stretch, and affect its warmth and structure.
• Silhouette and Fit: Designers need to choose the right silhouette based on the brand’s target audience and season. Whether you want oversized, slouchy sweaters or fitted, form-hugging knitwear, understanding how different yarns and stitch patterns behave is key to achieving the desired look.
• Functional Details: Features such as collars, cuffs, pockets, and closures (like buttons or zippers) add both functionality and visual interest. They must be carefully integrated into the knitwear during the production process to ensure a seamless finish.
Collaborating with your knitwear manufacturer early in the design process ensures that your ideas can be translated into high-quality, production-ready garments. Manufacturers can provide valuable insights into optimizing designs for efficient production while maintaining the desired look and feel.
Understanding Key Technical Aspects of Knitwear: Gauges and Needle Counts
In knitwear, gauge (GG) refers to the number of stitches per inch, and it plays a critical role in determining the thickness, weight, and overall texture of the fabric. The lower the gauge, the thicker and chunkier the fabric, while higher gauges result in finer and lighter fabrics. Each gauge serves different purposes in knitwear production and is suitable for specific garment types. Let’s break down the key gauges commonly used in the industry:
• 3-Gauge Knitwear (3GG):
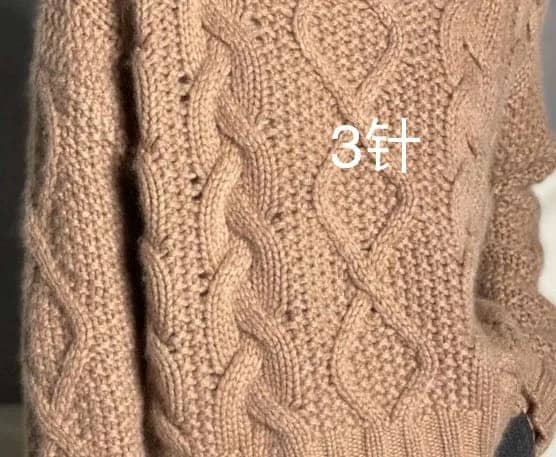
3GG is the lowest and thickest gauge typically used in knitwear manufacturing. This gauge produces extremely chunky and dense knit fabrics, making it perfect for heavy winter garments such as oversized sweaters, thick cardigans, and knit jackets. The large, visible stitches give garments a highly textured appearance, creating a cozy, hand-knit look. 3GG knitwear is ideal for outerwear or statement pieces that provide substantial warmth.
• 5-Gauge Knitwear (5GG):
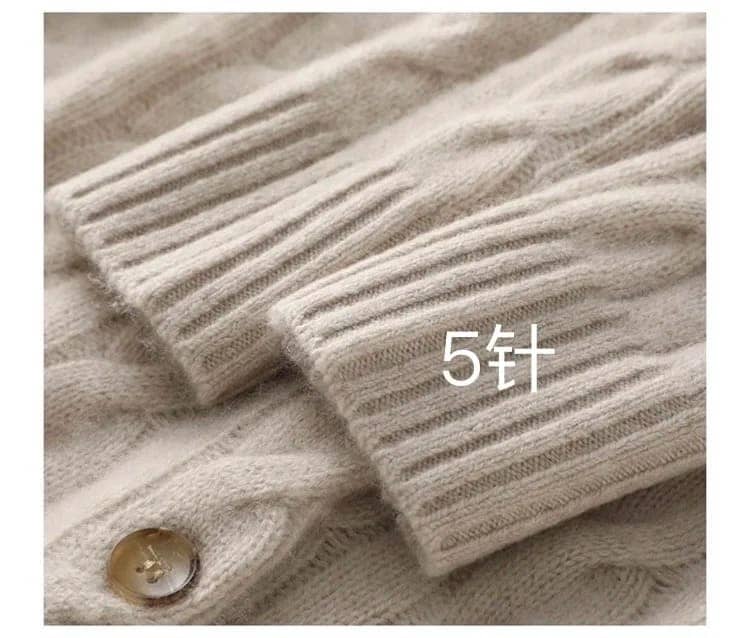
5GG strikes a balance between chunky and medium weight. It’s slightly less dense than 3GG but still provides considerable warmth and a textured finish. This gauge is commonly used for winter sweaters, cardigans, and accessories like scarves and hats. Knitwear in 5GG tends to look refined while still maintaining some bulk, making it versatile for both casual and more polished winter outfits.
• 7-Gauge Knitwear (7GG):
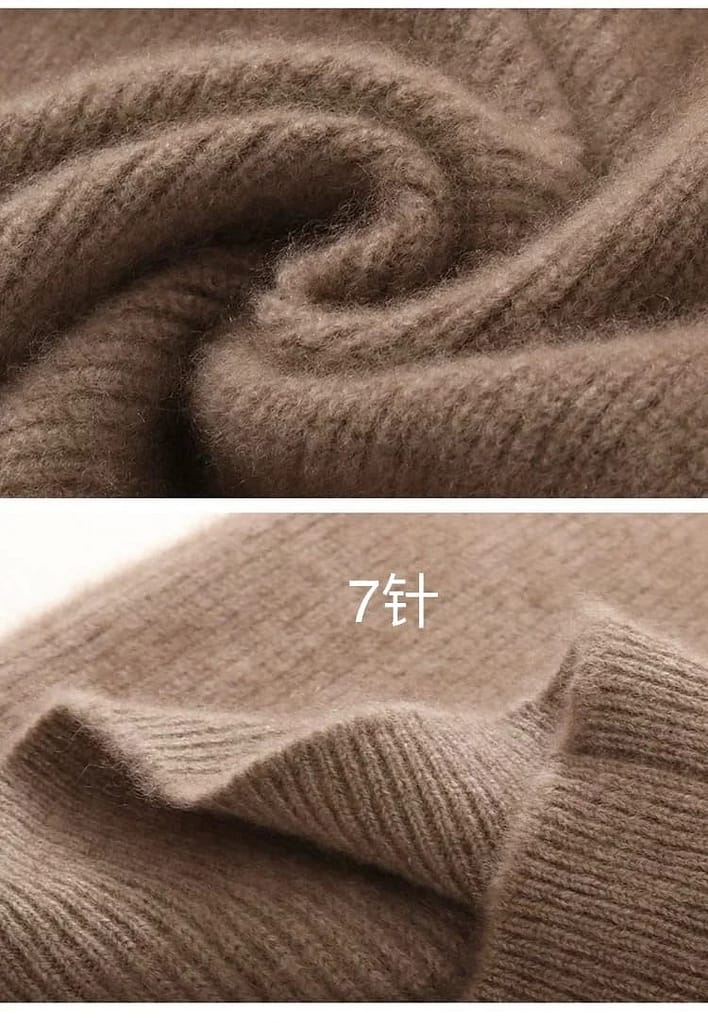
As mentioned earlier, 7GG produces a medium-thick fabric, perfect for colder seasons. It is often used for heavier sweaters, cardigans, and other knitwear that requires a balance between warmth and flexibility. The stitches are still somewhat visible, providing a tactile texture without the chunkiness of 3GG or 5GG knitwear.
• 12-Gauge Knitwear (12GG):
12GG knitwear is lighter and finer compared to lower gauges. This gauge creates a smoother, more refined fabric with smaller, less visible stitches. It is commonly used for transitional-season garments such as lightweight sweaters, turtlenecks, and layering pieces. Knitwear in 12GG offers more breathability and a closer fit, making it ideal for indoor wear or milder climates.
• 16-Gauge Knitwear (16GG):
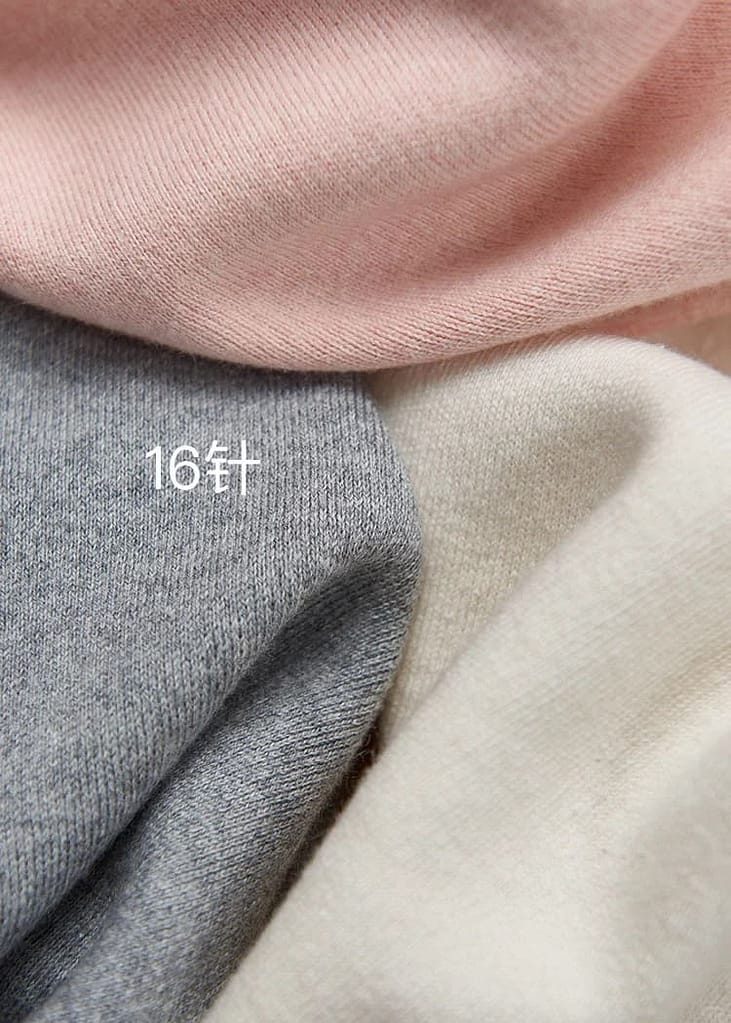
16GG is considered a fine-gauge knit and produces very thin, lightweight fabric. This high gauge is perfect for delicate knitwear, such as thin sweaters, cardigans, or even knit dresses that require a sleek, polished finish. Garments in 16GG are ideal for layering, especially in professional or warmer settings, where bulkier fabrics would be impractical. The fabric is smooth and highly flexible, offering a more tailored fit.
Each gauge has its advantages and is suited to different garment types and seasons:
• 3GG and 5GG: Ideal for chunky, heavy-knit garments meant for warmth and structure in winter wear.
• 7GG: A versatile, medium-weight gauge used for classic winter and fall garments, offering a balance of warmth and style.
• 12GG: A fine gauge, suited for lightweight knits and transitional garments that are more breathable and refined.
• 16GG: Ultra-fine and ideal for sophisticated, lightweight knitwear that requires a close fit and high attention to detail.
Needle Count and Its Impact
Needle count refers to the number of needles used in the knitting process and is closely related to gauge. The higher the needle count, the finer and more delicate the fabric produced. Lower needle counts create chunkier fabrics with larger stitches, as seen in lower gauges like 3GG and 5GG. High needle counts, used for fine gauges like 12GG and 16GG, result in smooth, intricate knitwear with minimal bulk.
The Knitwear Manufacturing Process: Step by Step
Knitwear production may seem simple at first glance, but creating a high-quality garment involves multiple intricate steps. From yarn preparation to the final quality check, each stage requires careful attention to detail. Let’s dive into the full production process:
Step 1: Winding the Yarn
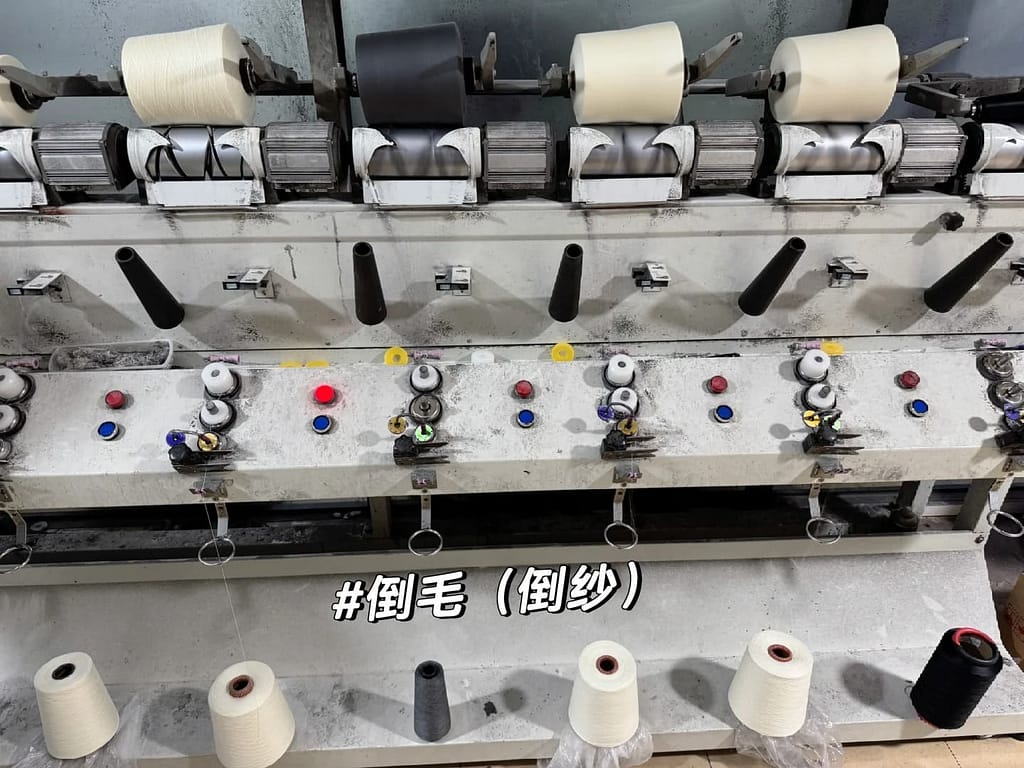
The process begins with preparing the yarn. Large yarn spools are wound into smaller spools to make them easier to work with during the knitting phase. During this step, the yarn undergoes a waxing treatment, which serves two purposes:
• Smoothing: Waxing the yarn makes it soft and smooth, reducing friction during machine knitting.
• Defect Removal: Any surface defects or impurities are removed from the yarn to ensure it’s ready for knitting. In some cases, the yarn is twisted or plied to meet the specific requirements of the garment design.
Step 2: Knitting
After the yarn is prepared, it’s time to start knitting. This process begins by setting up the garment’s design:
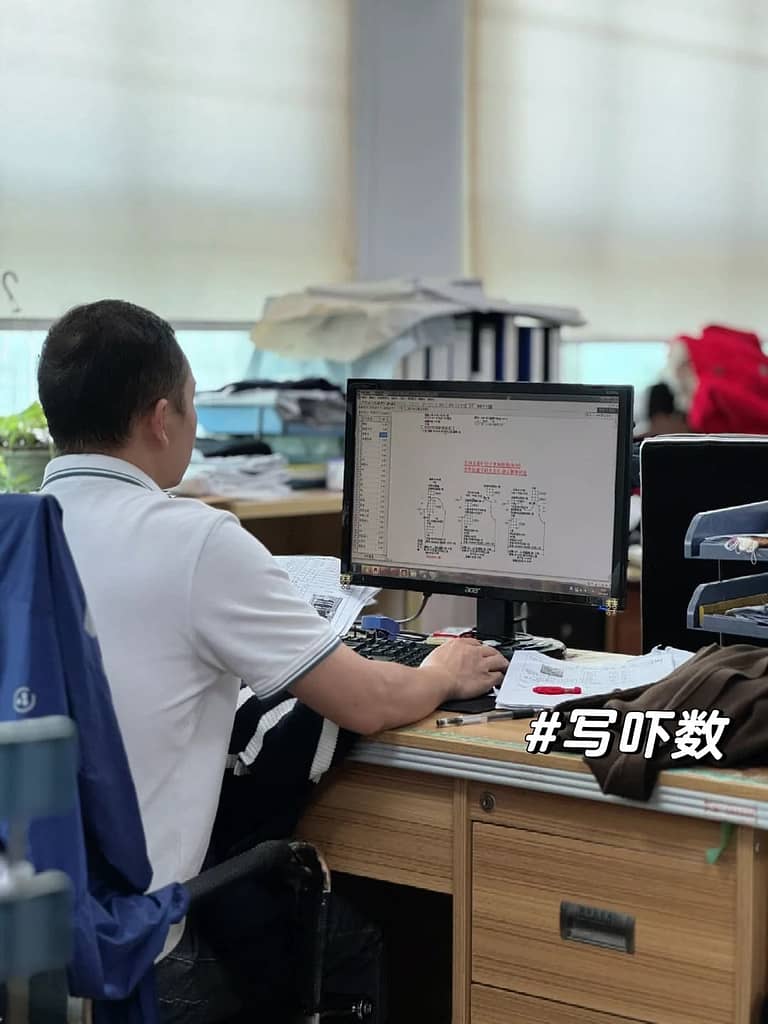
• Shape Setup: The garment’s shape, including the front, back, and sleeves, is determined based on the required specifications.
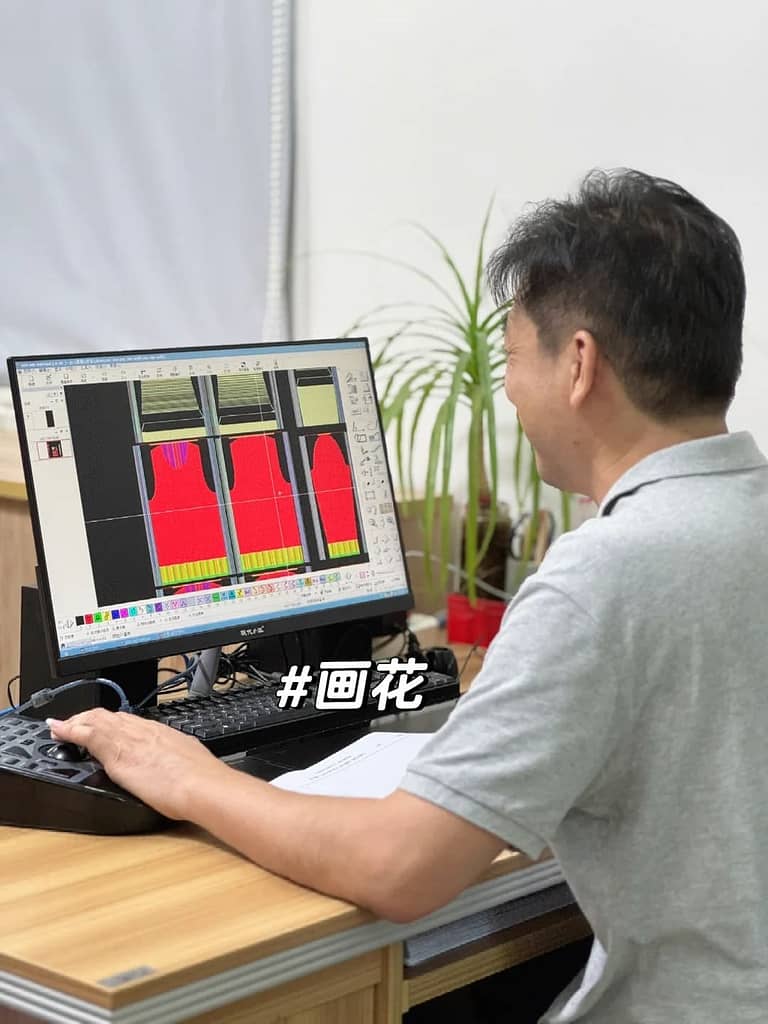
• Pattern Design: If the garment includes any patterns or textures, such as cables or jacquard designs, these are programmed into the knitting machines.
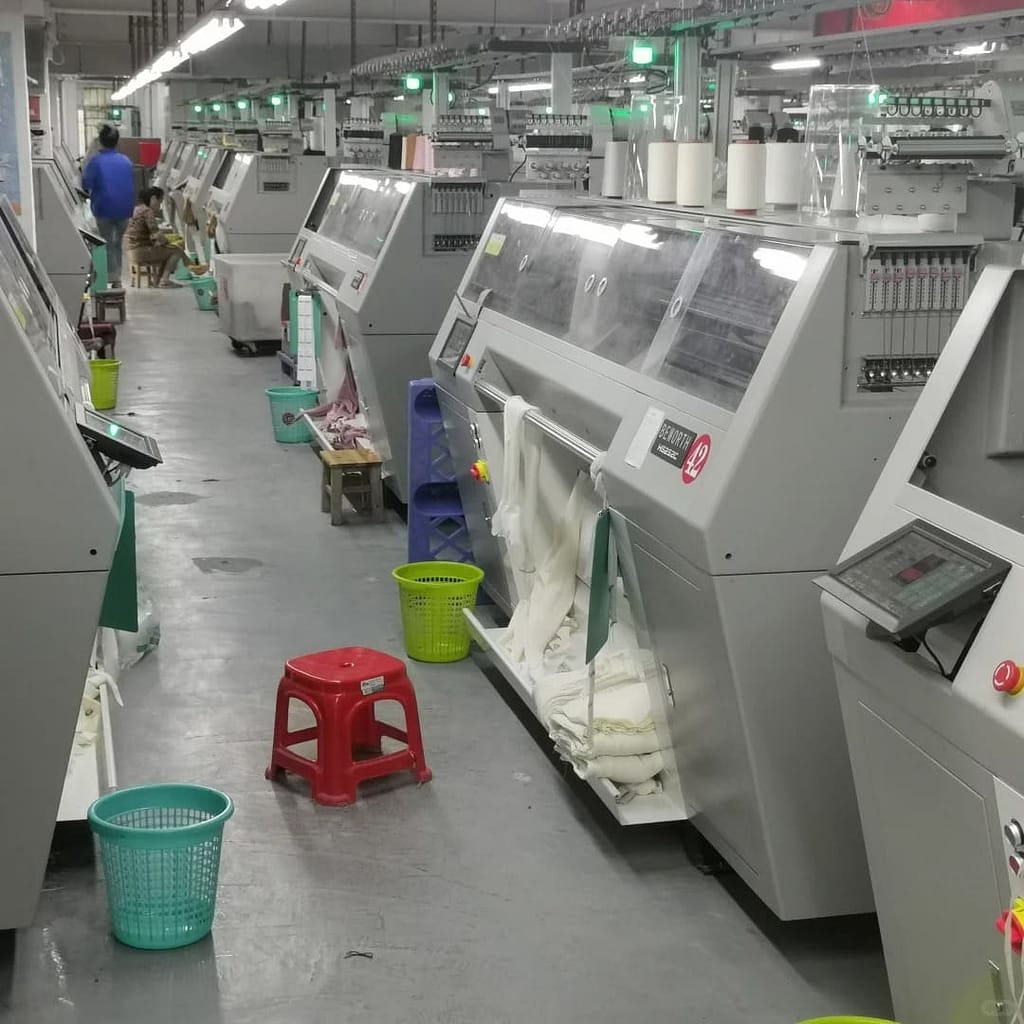
Once the program is ready, it’s input into a computerized knitting machine, which then knits the yarn into panels, such as the front and back pieces, sleeves, and other components. These panels are considered semi-finished products.
Step 3: Inspection of Knit Panels
Once the knitting process is complete, each panel is inspected carefully. This step ensures that the knitted fabric meets the desired quality and specifications before moving on to the garment assembly phase. Any defects found at this stage must be addressed before the panels proceed to the next step.
Step 4: Linking and Assembly
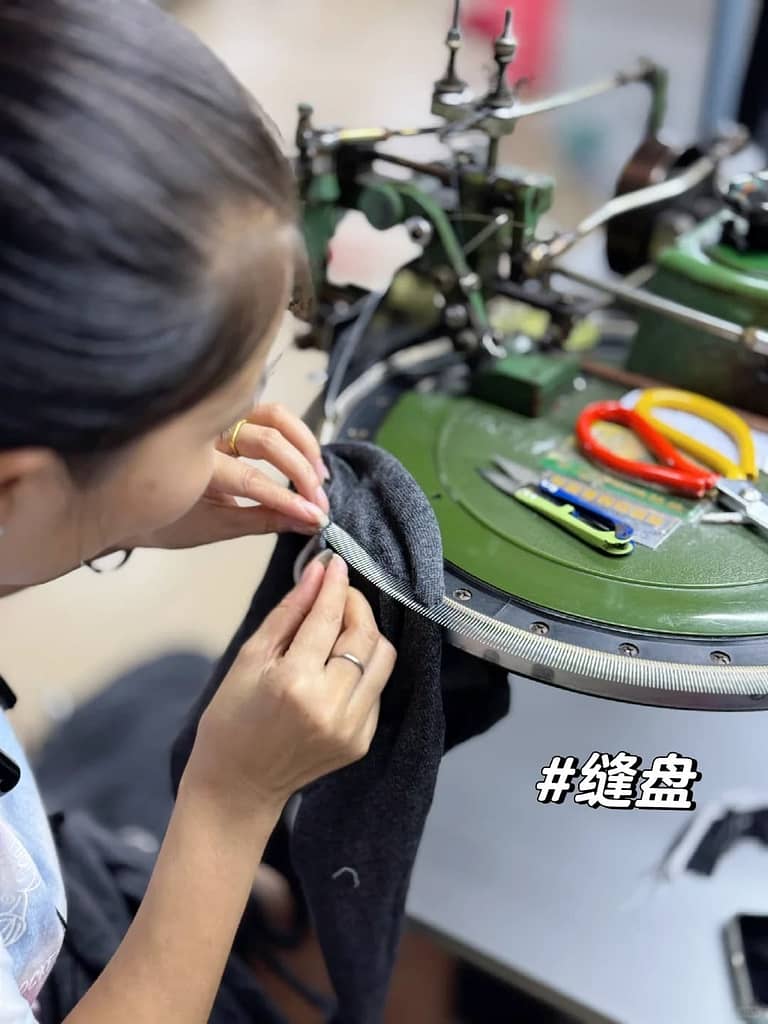
In this step, the individual panels (e.g., front, back, sleeves) are linked together to form the complete garment. This is done by carefully linking each stitch, loop by loop, using a technique called linking. This part of the process requires a high level of skill and attention, as any missed stitches can result in issues such as skipped stitches or unraveling. Proper linking is crucial for ensuring that the seams are smooth and durable.
Step 5: Threading and Finishing
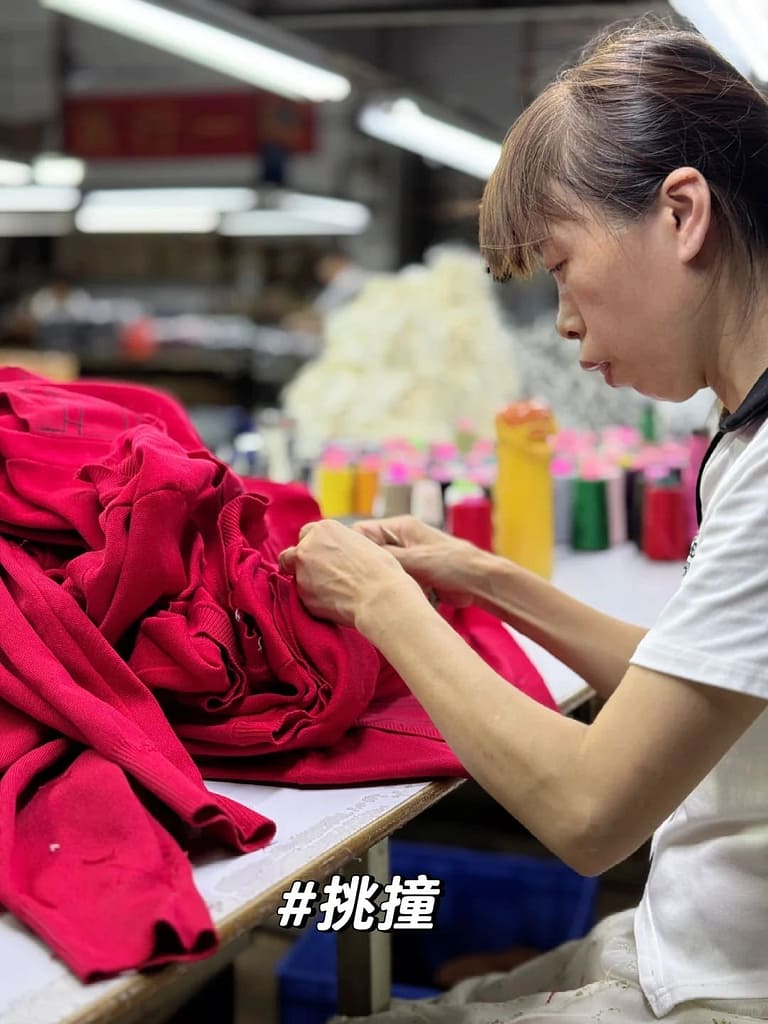
After the garment is assembled, any loose threads or yarn ends need to be carefully tucked into the fabric to prevent unraveling. This process, known as threading, is done manually. It involves using a needle to pull loose yarn into the knit to secure it. This step also includes handling areas where machine stitching isn’t possible, ensuring the garment is secure and polished.
Step 6: Quality Check Under Lighting

To guarantee the highest quality, each finished garment is placed under specialized lighting for inspection. This allows the production team to spot any missed stitches, uneven knitting, or pattern issues. If any defects are found, they are manually repaired before the garment moves forward. This ensures that only flawless pieces proceed to the final stages.
Step 7: Washing
Once the garment has passed inspection, it undergoes a washing process. Washing serves multiple purposes:
• Removing Odors: Any residual manufacturing odors are eliminated.
• Improving Fabric Feel: Washing softens the fabric and enhances its texture, making the garment more comfortable to wear.
• Controlling Shrinkage: This process also helps stabilize the fabric’s size, minimizing shrinkage after the garment is sold.
Step 8: Ironing and Shaping
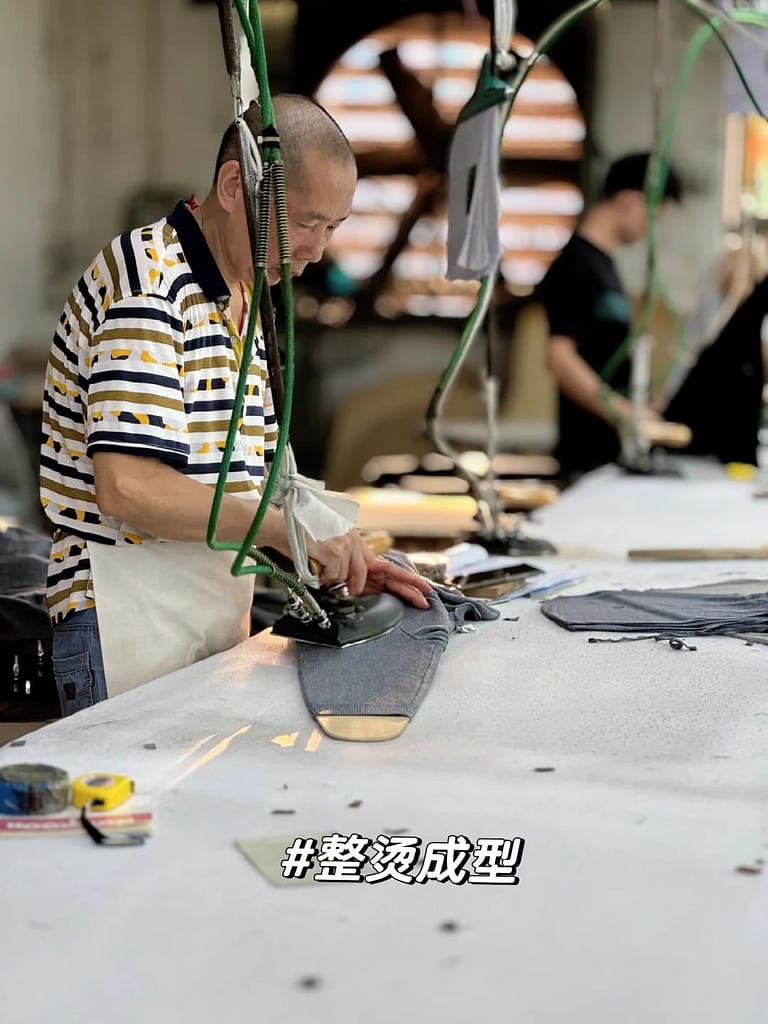
Knitwear, particularly garments made from elastic fibers like wool, requires careful pressing to achieve the desired shape and fit. During this step, the garment is placed on a template and steamed or ironed into its final shape. This ensures the knitwear holds its intended dimensions and the elasticity of the fabric is controlled. Pressing is essential for making sure the garment looks polished and fits well.
Step 9: Measurement
After pressing, the garment undergoes a precise measurement process. All parts of the garment, including the sleeves, chest, length, and collar, are measured to ensure they match the required specifications. If the garment does not meet the size chart, it may need to be adjusted or remade.
Step 10: Final Inspection and Packaging
Before packaging, the garment undergoes a final round of quality control. Each piece is inspected once more to ensure that there are no defects and that it meets all requirements. Once it passes this final check, the garment is ready for packaging. Custom labels and branded packaging are often added at this stage to create a professional finish.
While a sweater may appear simple, producing it requires careful attention to every detail through multiple complex steps. This process ensures that each piece of knitwear is of the highest quality, ready to meet the expectations of B2B buyers and consumers alike.
What to Look for in a Knitwear Manufacturer
For B2B buyers, choosing the right knitwear manufacturer is critical to ensuring high-quality products, meeting production timelines, and supporting brand growth. When evaluating potential manufacturing partners, there are several key factors to consider. Each of these can significantly impact the success of your sourcing process and the final product your brand delivers.
1. Quality Control Standards
One of the most important aspects of any knitwear manufacturer is their commitment to quality control. A reliable manufacturer will have rigorous inspection processes at every stage of production—from yarn selection to the final garment inspection. Key quality control aspects to look for include:
• Defect Inspection: The manufacturer should thoroughly inspect for issues such as skipped stitches, yarn defects, and sizing inaccuracies.
• On-Site Quality Control: Factories that perform on-site inspections ensure that every product adheres to your specifications before leaving the facility.
• Testing for Durability: High-quality knitwear manufacturers also conduct tests to ensure garments maintain their shape, color, and structural integrity after washing and wear.
Valtin Apparel, for instance, integrates quality control checks throughout the entire manufacturing process, ensuring each piece meets stringent quality requirements before it reaches your hands.
2. Fabric Variety and Customization Options
The ability to customize fabrics and designs is essential for brands looking to create unique products. A great manufacturer will offer a wide variety of fabric choices and the flexibility to create custom pieces tailored to your brand’s vision. Some considerations include:
• Yarn Options: Can the manufacturer provide the yarn materials you need, whether it’s a wool-cashmere blend or sustainable viscose?
• Design Customization: Are they able to incorporate custom stitching patterns, gauges, or designs to meet your specific product requirements?
• Labels and Packaging: The manufacturer should offer options for customized labels, hang tags, and packaging that align with your brand identity.
Working with a manufacturer located near a major fabric market, like Valtin Apparel in Guangzhou, ensures access to a wide range of fabric options, which is crucial for creating diverse, high-quality collections.
3. Experience and Expertise
A manufacturer’s experience in the knitwear industry can make a significant difference in both the quality of your products and the efficiency of the production process. Experienced manufacturers are more likely to:
• Understand Complex Designs: They can handle intricate knitwear patterns and structures, from fully fashioned knitting to jacquard designs.
• Problem-Solving Capabilities: Years of experience allow them to troubleshoot potential production issues before they impact timelines.
• Adapt to Market Trends: Experienced manufacturers stay up to date with the latest knitwear technologies and fashion trends, helping your brand stay competitive.
Valtin Apparel’s expertise in knitwear manufacturing allows us to produce a wide range of garments, from casual hoodies to luxury sweaters, tailored to meet the specific needs of your brand.
4. Sustainability Practices
With the rising demand for sustainable fashion, choosing a manufacturer that incorporates eco-friendly practices is a significant consideration for many brands. A sustainable knitwear manufacturer might offer:
• Eco-Friendly Materials: They provide access to organic cotton, recycled polyester, and biodegradable fibers like viscose.
• Responsible Production Processes: They minimize waste, use eco-friendly dyes, and ensure ethical labor practices.
• Certifications: Look for manufacturers that have relevant certifications like GOTS (Global Organic Textile Standard) or OEKO-TEX®, which ensure that the materials and processes meet high environmental and safety standards.
At Valtin Apparel, we’re committed to offering sustainable yarn options and following responsible production methods, ensuring our clients can meet their sustainability goals.
5. Efficiency and Delivery Time
Timely delivery is crucial for staying ahead of seasonal fashion trends or ensuring stock is available when your customers need it. A reliable manufacturer should have:
• Clear Production Timelines: Make sure the manufacturer can clearly communicate how long each stage of production will take, from sampling to bulk manufacturing.
• Flexible MOQ (Minimum Order Quantity): For growing brands, flexible MOQ options allow you to produce smaller runs of custom designs without overcommitting to large inventories.
• On-Time Shipping: Delayed shipments can hurt your business, so it’s important to work with manufacturers who have a track record of meeting deadlines.
Valtin Apparel offers transparent production timelines, with sample delivery within 10-14 days and bulk production times of 28-35 days. We ensure efficient delivery and maintain close communication with clients to prevent any disruptions in supply chains.
By considering these factors—quality control, customization, experience, sustainability, and efficiency—you can make a more informed decision when selecting a knitwear manufacturer. The right partner will not only produce high-quality garments but will also support your brand’s growth by offering flexibility, reliability, and expert craftsmanship.
Why Customization Matters in Knitwear for Growing Brands
For emerging brands, customization is not just an option—it’s a crucial strategy for standing out in a crowded market. In today’s competitive fashion landscape, customers expect more than just high-quality clothing; they seek unique designs that reflect their personal style or a brand’s distinctive identity. Customization in knitwear manufacturing allows growing brands to offer exclusive pieces that differentiate them from mass-market options and build brand loyalty.
Here’s why customization is key to the success of growing knitwear brands:
1. Unique Designs to Define Your Brand
Customization enables brands to create knitwear that is truly unique. Whether it’s a specific stitch pattern, a custom logo, or a one-of-a-kind colorway, offering something different from competitors helps establish a strong brand identity.
• Custom Stitch Patterns and Textures: Knitting allows for endless creative possibilities. You can choose from a wide range of stitch techniques, such as ribbing, cabling, and jacquard, to create textures that set your brand apart. Custom designs make your products instantly recognizable to consumers.
• Exclusive Color Palettes: Color is a powerful tool for brand recognition. By offering custom-dyed yarns in your brand’s signature shades, you can create knitwear that feels cohesive with your overall brand aesthetic.
• Branded Embellishments: Logos, tags, or embroidery can be seamlessly integrated into knitwear. These custom touches not only reinforce your brand identity but also add a premium feel to your products.
At Valtin Apparel, we offer a range of customization options to help brands create standout knitwear that speaks directly to their audience.
2. Tailored Fit and Styles
Offering customizable sizing and fit options is another advantage that can attract a broader customer base. As consumer expectations shift towards more personalized fashion, knitwear that is designed to fit specific body types or style preferences becomes increasingly important.
• Custom Fit Adjustments: Whether your customers prefer oversized sweaters or fitted cardigans, customization allows you to offer multiple fit options. A reliable manufacturer will help you adjust patterns for different body shapes and sizes without compromising on quality or design.
• Style Versatility: From relaxed, casual styles to more formal, structured pieces, customization lets you create knitwear that aligns with the specific lifestyle or target demographic of your brand.
Offering customized fit options is especially valuable for emerging brands looking to establish a reputation for inclusivity and customer care.
3. Small Minimum Order Quantities (MOQs) for Flexibility
Growing brands often face the challenge of balancing inventory with demand. Large-scale manufacturers typically require high minimum order quantities, making it difficult for smaller brands to experiment with new designs or introduce a variety of styles.
However, manufacturers like Valtin Apparel offer flexible MOQs, which allow brands to test custom designs without the risk of overproduction. This flexibility enables brands to:
• Experiment with New Designs: Launch small batches of customized knitwear to test market response before committing to larger production runs.
• Reduce Inventory Risks: Manage cash flow more effectively by producing only what is needed, minimizing the risk of excess stock.
• Introduce Seasonal or Limited-Edition Pieces: Offer exclusive, limited-run collections that create a sense of urgency and exclusivity among customers.
This approach is ideal for growing brands looking to maintain agility in a fast-paced market while offering a wide variety of custom designs.
4. Custom Labels and Packaging
Beyond the product itself, the way knitwear is presented to customers plays a significant role in shaping their experience with your brand. Custom labels, hang tags, and packaging elevate your brand and give it a professional, polished look. These elements are an opportunity to communicate your brand values, tell your story, and create a memorable unboxing experience.
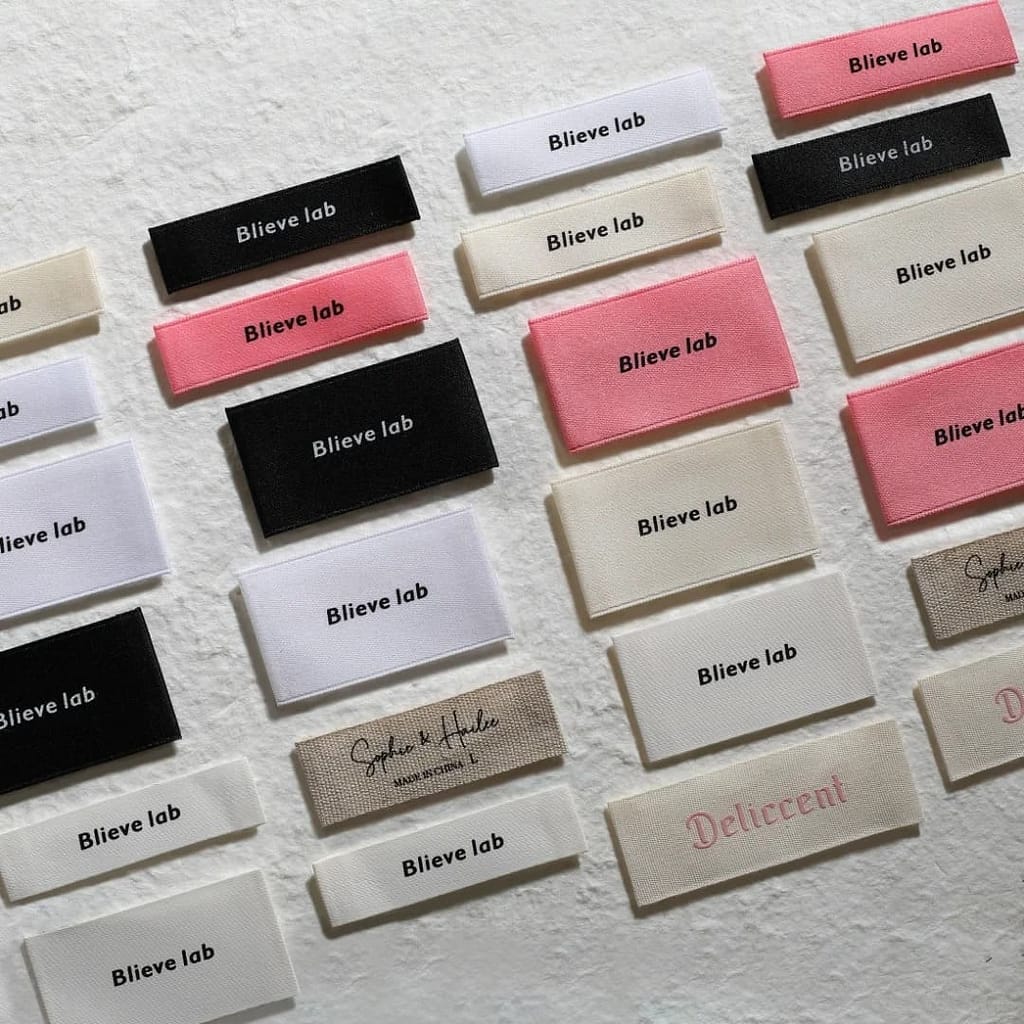
• Custom Labels: Add branded labels that align with your brand’s ethos, whether it’s eco-friendly materials, minimalist designs, or luxurious finishing touches.
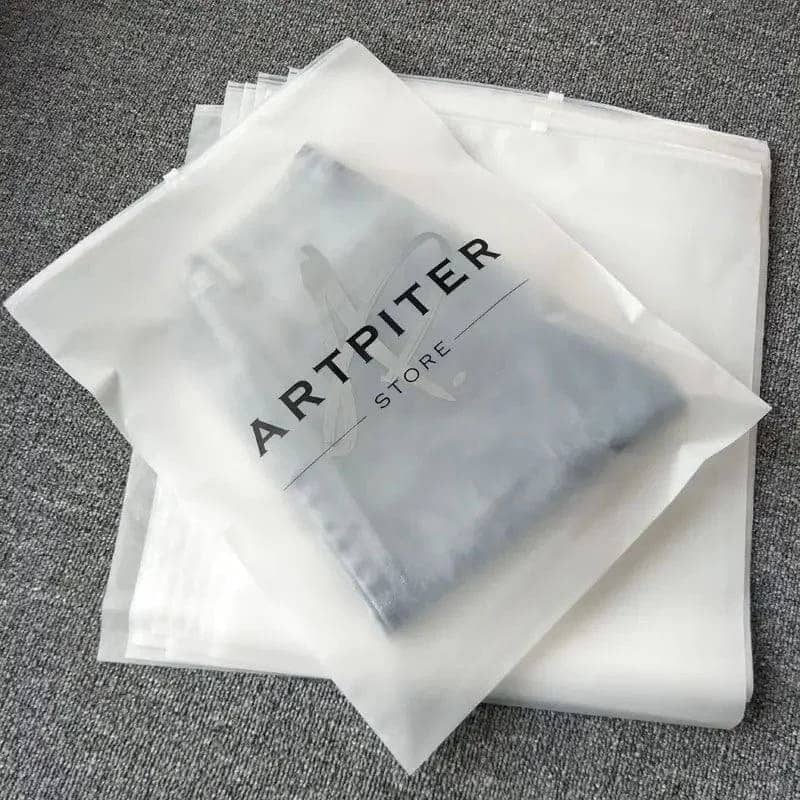
• Branded Packaging: From boxes to bags, offering packaging that reflects your brand’s identity strengthens customer loyalty and makes a lasting impression.
Many manufacturers, including Valtin Apparel, offer end-to-end solutions, providing not just customized garments but also custom labeling and packaging options to enhance your brand’s presentation.
Incorporating customization into your knitwear offerings not only helps differentiate your brand but also allows you to respond to customer demand with flexibility and creativity. At Valtin Apparel, we specialize in providing the customization options and low MOQs needed to help emerging brands scale effectively, whether you’re launching a new collection or creating exclusive pieces for your audience.
Partnering with the Right Knitwear Manufacturer
Choosing the right knitwear manufacturer is a pivotal decision for any B2B buyer. The manufacturer you partner with will not only influence the quality of your products but also your ability to deliver on time, scale efficiently, and meet your brand’s unique needs. For growing brands, finding a manufacturer that offers flexibility, expertise, and reliable communication is crucial to long-term success.
Here’s what to look for when selecting the right knitwear manufacturing partner:
1. Proven Expertise in Knitwear Manufacturing
A manufacturer with deep expertise in knitwear production will be able to guide you through the process, from selecting the best yarn to troubleshooting any potential production issues. Experienced manufacturers understand the complexities of different knitting techniques and fabric types, allowing them to provide better results.
• Technical Knowledge: Look for a manufacturer that can handle a wide range of knitwear styles, from heavy-gauge sweaters to fine-gauge cardigans. They should be able to offer solutions for different designs, gauges, and stitch patterns.
• Portfolio of Successful Projects: A manufacturer with a proven track record can demonstrate their ability to produce high-quality knitwear. Ask for examples of previous work or case studies that show their expertise in producing garments similar to what you need.
Valtin Apparel has years of experience in knitwear manufacturing, producing everything from casual hoodies and sweaters to luxury knits for premium brands. Our ability to deliver high-quality products across different knitwear styles makes us a trusted partner for brands of all sizes.
2. Customization Capabilities
As mentioned earlier, customization is key for emerging brands looking to differentiate their offerings. A manufacturer with strong customization capabilities will help you bring your design vision to life, whether you’re looking for custom stitch patterns, labels, or yarn choices.
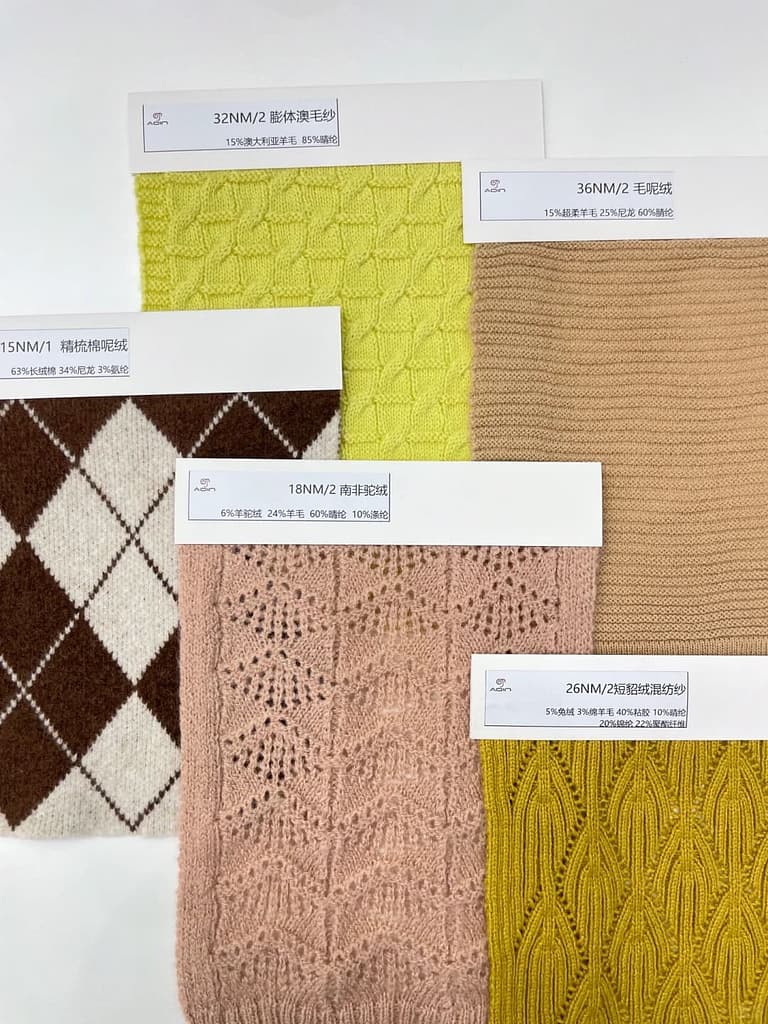
• Flexibility in Design: Choose a manufacturer that can accommodate a range of customization options, from color choices to pattern complexity. Whether you want fully fashioned knitting for a tailored fit or specific design elements like jacquard patterns, your manufacturer should be able to handle the intricacies of your design.
• Yarn Variety: Access to a wide range of yarns, including natural, synthetic, and sustainable options, ensures that you can create the right product for your target market. A manufacturer who can source specific yarns and offer advice on the best materials for your designs is invaluable.
At Valtin Apparel, we provide extensive customization options to match your brand’s needs. With access to a wide selection of fabrics and yarns, we can help you create products that are uniquely tailored to your specifications.
3. Transparent Communication and Collaboration
Clear and consistent communication is vital to ensuring the production process runs smoothly. You need a manufacturer that provides regular updates, is responsive to your inquiries, and is proactive in addressing any potential issues.
• Dedicated Account Managers: Having a single point of contact ensures that communication is streamlined. An account manager who understands your brand and needs will be able to provide timely updates and ensure that your requirements are met throughout the production process.
• Collaborative Approach: The best manufacturers act as partners rather than just suppliers. They should offer suggestions on design improvements, help troubleshoot production challenges, and work with you to optimize the manufacturing process.
At Valtin Apparel, we pride ourselves on maintaining open lines of communication with our clients. Our dedicated account managers work closely with you to ensure that your project stays on track and that any concerns are addressed promptly.
4. Reliable Production Timelines
In the fast-paced world of fashion, meeting deadlines is critical to your brand’s success. A manufacturer that can deliver on time ensures that your products are available when needed, whether you’re launching a new collection or restocking popular items.
• Clear Production Schedules: Choose a manufacturer that provides clear timelines for sampling, production, and shipping. They should be able to give you accurate estimates on how long each stage of production will take.
• Ability to Meet Deadlines: Delays in production can cost your business in lost sales and missed opportunities. A manufacturer with a track record of meeting deadlines will help you avoid these pitfalls.
Valtin Apparel guarantees timely production and delivery, with sample delivery times of 10-14 days and bulk production completed within 28-35 days. We understand how crucial it is to meet seasonal demands and work hard to ensure that your products arrive on time.
5. Scalable Manufacturing Capacity
As your brand grows, your production needs will change. A manufacturer with scalable capacity can accommodate your growth, whether you’re producing small, custom batches or scaling up to meet higher demand. A flexible partner will be able to adjust production volumes based on your evolving needs.
• Low Minimum Order Quantities (MOQs): For smaller or growing brands, having the option to produce in smaller quantities is essential for managing inventory risk and testing new designs.
• Ability to Scale: As your brand grows, you’ll need a manufacturer who can handle larger production runs without compromising quality or timelines. A scalable manufacturer ensures you won’t need to switch partners as your production needs increase.
Valtin Apparel offers flexible MOQs, starting at 200 pieces per style, with the capability to scale up as your business grows. This allows you to start small and expand confidently as your brand gains traction in the market.
Partnering with the right knitwear manufacturer is essential for ensuring your products meet the highest standards of quality, fit, and design. A reliable manufacturer, like Valtin Apparel, will not only provide technical expertise and customization options but will also collaborate closely with you to meet deadlines and support your brand’s growth.
Conclusion
Mastering the knitwear manufacturing process is crucial for B2B buyers looking to deliver high-quality, customized garments to their customers. From understanding the technical aspects of knitting, such as gauges and needle counts, to selecting the right yarn and manufacturer, every decision impacts the success of your brand. Choosing a partner who can offer expertise, flexibility, and efficient production timelines will help you stay competitive in the fast-paced fashion market.
At Valtin Apparel, we specialize in producing premium, customizable knitwear tailored to your brand’s unique needs. With years of experience, access to high-quality fabrics, and a commitment to excellence, we are ready to help your brand grow and succeed in the ever-evolving world of fashion.