Understanding T-shirt production costs is crucial whether you’re starting a clothing brand or optimizing an existing business. Factors like fabric type, printing method, labor costs, and manufacturing location all play a significant role in determining the final price.
Key Takeaways:
- Fabric & printing methods impact cost the most—cotton is more expensive than polyester, and screen printing is cheaper for bulk orders.
- Manufacturing location affects labor costs—countries like China and Bangladesh offer lower production costs, while the USA and Europe focus on premium quality.
- Bulk production reduces the per-unit cost, but small-batch production is better for testing new designs.
- Hidden costs like shipping, packaging, and branding should be factored into your budget.
- Cost-saving strategies include bulk fabric purchasing, negotiating with suppliers, and using affordable printing methods.
By carefully analyzing your production costs and making smart business decisions, you can maximize profit without sacrificing quality.
Cost Breakdown of Making a T-Shirt
When calculating T-shirt production costs, it’s essential to break down all the factors that contribute to the final price. Here’s a detailed look at the main cost components:
Material Costs
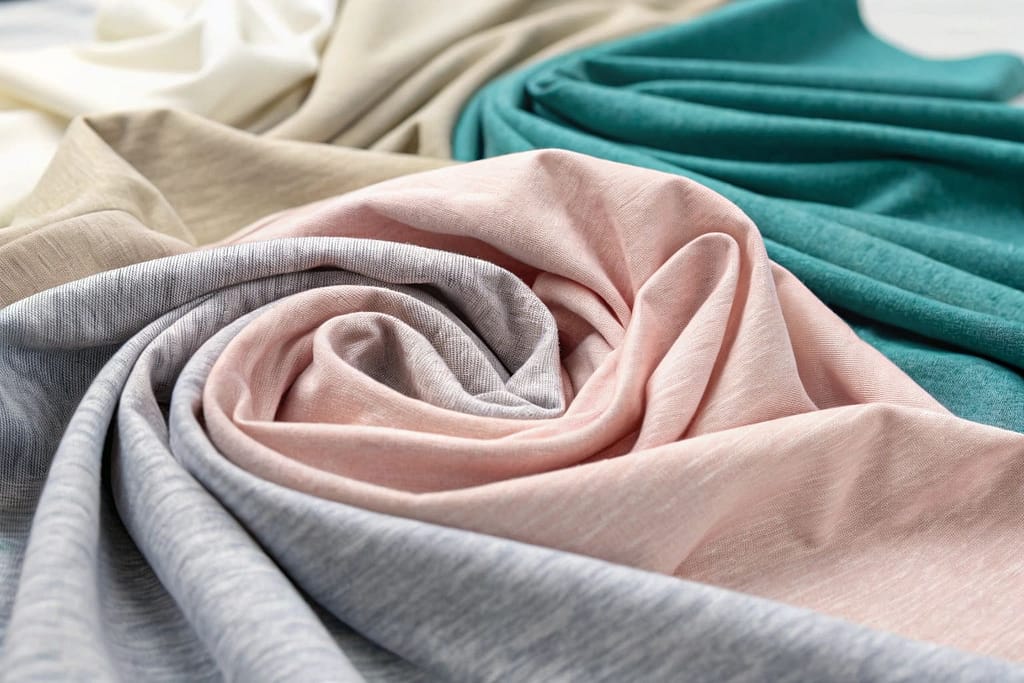
The type of fabric used significantly impacts the cost of making a T-shirt. Common options include:
- Cotton ($1 – $5 per T-shirt) – The most popular and breathable fabric. Organic cotton costs more than regular cotton.
- Polyester ($2 – $6 per T-shirt) – Cheaper than cotton, durable, but less breathable.
- Blends ($3 – $7 per T-shirt) – A mix of cotton and polyester, balancing cost, comfort, and durability.
- Specialty Fabrics ($5 – $15 per T-shirt) – Bamboo, hemp, or moisture-wicking athletic materials cost more.
Labor Costs
Labor costs vary depending on where the T-shirt is manufactured:
- USA & Europe ($5 – $15 per T-shirt) – Higher wages lead to increased production costs.
- China, India, Bangladesh ($1 – $5 per T-shirt) – Lower labor costs make manufacturing cheaper.
- Ethical & Fair Trade Production ($6 – $20 per T-shirt) – Companies that ensure fair wages and safe working conditions charge more.
- Global Wage Report – Compare labor costs by country.
Printing & Design Costs
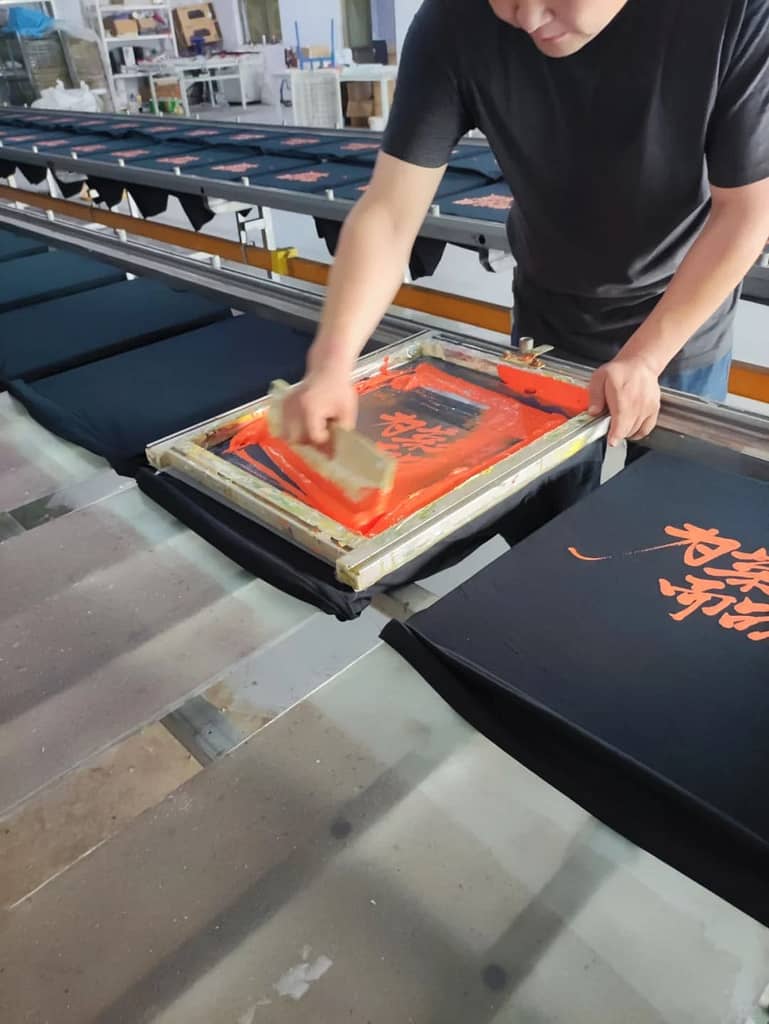
The printing method plays a big role in final pricing:
- Screen Printing ($1 – $5 per T-shirt) – Cost-effective for bulk orders but expensive for small runs.
- Direct-to-Garment (DTG) ($3 – $7 per T-shirt) – Great for custom and small-batch orders but more expensive per unit.
- Embroidery ($1 – $5 per T-shirt) – High-quality but labor-intensive, making it a good option.
Packaging & Labeling
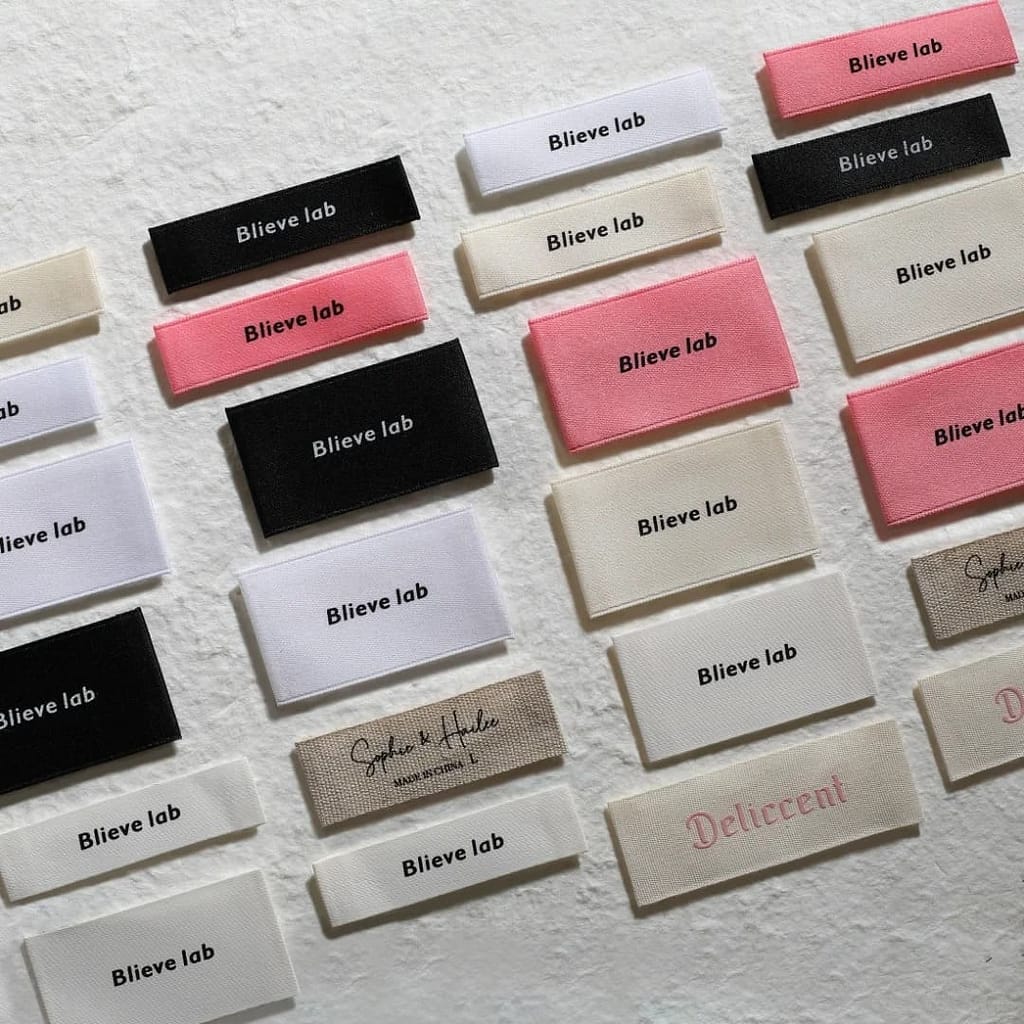
Packaging and branding affect overall expenses:
- Basic Packaging ($0.10 – $0.80 per T-shirt) – Simple polybags or plain boxes.
- Branded Packaging ($1 – $5 per T-shirt) – Custom boxes, tissue paper, and stickers for premium branding.
- Custom Labels & Tags ($0.30 – $2 per T-shirt) – Adds professionalism but increases costs.
Fixed vs. Variable Costs
When producing T-shirts, it’s essential to understand the difference between fixed costs and variable costs to calculate profitability and pricing accurately.
Fixed Costs (One-Time or Recurring Business Expenses)

These are expenses that remain constant regardless of how many T-shirts you produce.
- Equipment & Machinery ($500 – $50,000+)
- Screen printing machines
- DTG printers
- Embroidery machines
- Factory or Warehouse Rent ($500 – $5,000/month)
- Varies based on location and production scale.
- Business Licensing & Compliance ($50 – $1,000 per year)
- Required permits and legal fees depending on the country.
Variable Costs (Changes Based on Production Volume)
These costs fluctuate depending on the number of T-shirts produced.
- Fabric & Materials ($1.5 – $15 per T-shirt)
- Higher quality fabric increases production costs. For more information on t-shirt fabrics, check out my previous post.
- Labor Costs ($1 – $15 per T-shirt)
- Wage costs vary based on country and production type.
- Printing & Embellishments ($1 – $15 per T-shirt)
- Bulk orders reduce cost per unit. Different printing methods and printing materials affect the price.
- Shipping & Logistics ($0.50 – $10 per T-shirt)
- International shipping adds significant costs. Sea freight is slow and cheap; air freight is fast and expensive.
Key Takeaway
- If you’re producing small batches, fixed costs can make production expensive.
- Bulk production reduces the impact of fixed costs, lowering overall costs per T-shirt.
Manufacturing Location Impact
Where you manufacture your T-shirts has a huge impact on production costs. Labor costs, material availability, and ethical considerations all vary by location. Here’s a breakdown of how different countries compare:
Cost Comparison by Country
Country | Labor Cost Per T-Shirt | Average Total Production Cost | Pros | Cons |
---|---|---|---|---|
USA | $5 – $15 | $7 – $25 | High quality, local production, fast shipping | Expensive labor, higher material costs |
China | $1 – $5 | $3 – $10 | Low labor costs, large-scale production | Shipping times, import duties |
India | $1 – $4 | $2 – $8 | Affordable labor, strong textile industry | Quality can vary |
Bangladesh | $0.50 – $3 | $2 – $6 | Ultra-low costs, large manufacturing capacity | Ethical concerns, long shipping times |
Europe | $6 – $20 | $10 – $30 | Premium quality, ethical standards | High labor costs |
Ethical & Sustainable Manufacturing Costs
Eco-friendly and ethical production often costs 30-50% more due to fair wages, organic materials, and sustainable practices.
- Organic Cotton T-Shirts – $7 – $20 per shirt
- Fair Trade Certified Factories – $8 – $25 per shirt
- Carbon-Neutral & Low-Waste Manufacturing – Adds $1 – $5 per shirt
Key Takeaway
- For the lowest costs, China, India, and Bangladesh are the best options.
- For premium quality and fast shipping, the USA and Europe are ideal.
- For sustainable and ethical production, be prepared to pay a premium.
Bulk Production vs. Small Batch
One of the biggest factors affecting T-shirt production costs is the order quantity. Large-scale manufacturing significantly reduces the cost per unit, while small-batch production offers flexibility but at a higher price.
Cost Comparison: Bulk vs. Small Batch
Order Quantity | Cost Per T-Shirt (Basic 160GSM Cotton, Screen Print) | Total Production Cost |
---|---|---|
10 – 50 shirts | $8 – $15 per shirt | $80 – $750 |
100 – 500 shirts | $5 – $10 per shirt | $500 – $5,000 |
1,000 – 5,000 shirts | $3 – $7 per shirt | $3,000 – $35,000 |
10,000+ shirts | $1.50 – $5 per shirt | $15,000+ |
Benefits of Bulk Production
Lower Cost Per Unit – More shirts = reduced manufacturing cost per piece.
Better Supplier Deals – Bulk orders often get discounts on materials.
Consistent Quality – Large factories have better production consistency.
When Small Batch Production Makes Sense
Testing New Designs – Great for launching new collections without high upfront costs.
Limited Edition or Custom Orders – Best for premium, handmade, or niche brands.
Print-on-Demand Business Model – No inventory costs, but higher production cost per unit.
Key Takeaway
- For businesses scaling up, bulk production offers major cost savings.
- For new or niche brands, small batch orders help minimize risk while testing the market.
Additional Costs to Consider
Beyond fabric, printing, and labor, several hidden costs can impact T-shirt production costs. These expenses are often overlooked but can add up quickly.
Shipping & Logistics
- Domestic Shipping ($0.50 – $5 per shirt) – Faster delivery but higher costs for small orders.
- International Shipping ($3 – $15 per shirt) – Cheaper in bulk but may include customs fees.
- Freight Costs ($500 – $5,000 per shipment) – Large orders often require freight shipping via sea or air.
Marketing & Branding Costs
- Website & E-commerce Setup ($100 – $5,000) – Shopify, WooCommerce, or custom websites.
- Advertising ($500 – $10,000 per month) – Facebook Ads, Google Ads, influencer marketing.
- Professional Photography ($100 – $1,000 per session) – Quality product images increase sales.
Taxes & Import Duties
- Import Taxes (5-20% of total cost) – Varies by country.
- Business Taxes (Varies) – Income tax, VAT, or sales tax, depending on location.
Key Takeaway
- For local production, shipping and import duties are minimal.
- For international orders, factor in freight costs and taxes to avoid unexpected expenses.
How to Reduce T-Shirt Production Costs
Keeping T-shirt production costs low while maintaining quality is crucial for profitability. Here are smart strategies to save money:
Choose Cost-Effective Materials
- Use Cotton-Polyester Blends – Cheaper than 100% cotton but still comfortable.
- Buy Fabric in Bulk – Larger purchases reduce per-yard costs.
Optimize Printing & Production
- Screen Printing for Bulk Orders – Cheaper for large quantities than DTG.
- Limit Colors & Designs – Fewer colors = lower printing costs.
- Use Heat Transfers for Small Batches – Affordable for small, custom designs.
Work with the Right Manufacturer
- Compare Multiple Suppliers – Get quotes from different factories.
- Negotiate Bulk Discounts – Most manufacturers lower prices for large orders.
- Consider Overseas Production – Countries like China, India, and Bangladesh offer lower labor costs.
Reduce Shipping & Logistics Costs
- Order in Bulk to Minimize Shipping Fees – Fewer shipments = lower overall costs.
- Use Local Manufacturers for Small Orders – Avoid high international shipping fees.
- Plan Inventory in Advance – Prevent rush shipping costs.
Avoid Unnecessary Extras
- Skip Expensive Packaging – Basic packaging saves money.
- Use Digital Marketing Instead of Expensive Ads – Social media marketing can be free or low-cost.
Key Takeaway
By optimizing materials, choosing the right production method, and negotiating with suppliers, you can cut costs without sacrificing quality.
FAQs
1. What is the cheapest way to produce T-shirts?
The cheapest way to produce T-shirts is by using bulk production in a low-cost country like China, India, or Bangladesh. Using screen printing for large orders, cotton-polyester blends, and simple designs also helps reduce costs.
2. How much does it cost to make a T-shirt in bulk?
For basic cotton T-shirts, bulk production costs range from $1.50 – $7 per shirt, depending on fabric quality, location, and printing method. The more you order, the lower the price per unit.
3. Is it cheaper to manufacture locally or overseas?
Overseas manufacturing (China, India, Bangladesh) is cheaper due to lower labor costs, but shipping and import taxes can add expenses. Local production (USA, Europe) is more expensive but offers faster delivery and higher quality control.
4. What affects the price of a custom T-shirt?
The price of a custom T-shirt depends on:
Fabric type – Organic cotton costs more than polyester.
Printing method – DTG and embroidery are pricier than screen printing.
Order quantity – Larger orders lower the price per unit.
Branding & packaging – Custom labels and premium packaging increase costs.